6026
15 min
Everything You Need to Know About Supply Chain Management (SCM)

Supply Chain Management (SCM) is the backbone of any business that produces and sells goods. In the global economy, it organizes collaboration across multiple stakeholders and geographies.
This article will look at the details of SCM, covering key parts like procurement, production, order fulfillment, and after-sales support. We'll also talk about the challenges and opportunities, including the use of new technologies and the move towards sustainability. Whether you're experienced or new to the field, this guide will help you understand all aspects of supply chain management.
Definition of Supply Chain Management
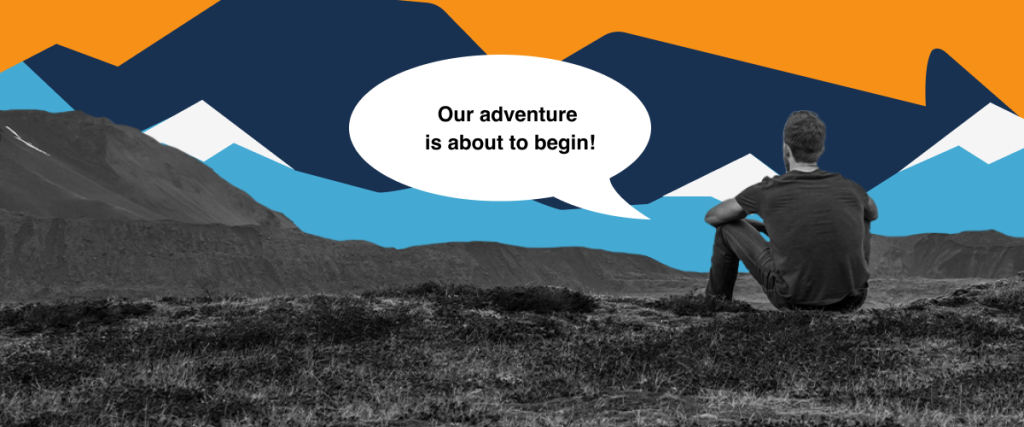
Supply Chain Management (SCM) is a systematic approach to managing the entire flow of information, materials, and services from raw material suppliers through factories and warehouses to the end customer.
It involves planning and managing all activities in sourcing, procurement, and logistics. SCM also includes coordination and collaboration with channel partners, which can be suppliers, intermediaries, third-party service providers, and customers. In essence, SCM brings together supply and demand management within and between companies to provide the best value to customers at the lowest cost for the whole supply chain.
Importance and Relevance in Modern Business
An an era where markets are global, competition is fierce, and customer expectations are higher than ever, SCM is essential for a company's success. Here's why SCM is so important:
- Strategic competitive advantage. By ensuring efficient operations, companies can reduce costs and offer better prices or higher quality products than their competitors.
- Customer satisfaction. Customers expect quick and reliable service, and SCM is key to meeting those expectations.
- Agility and adaptability. SCM allows companies to be more adaptable in their operations, quickly responding to changes such as fluctuations in demand.
- Cost reduction. Effective management optimizes the production and distribution process, which can reduce costs. This includes minimizing waste, reducing inventory costs, and improving procurement processes.
- Enhanced efficiency. SCM streamlines operations, making them more efficient. It reduces the time from production to market.
- Risk management. Systematic approach helps identify potential risks in the supply chain and develop strategies to mitigate them, ensuring business continuity.
- Sustainability. Companies are using SCM to minimize the environmental footprint and promote fair labor practices.
SCM influences everything from day-to-day operations to long-term strategic planning. It's a complex field that requires a deep understanding of multiple factors, but when executed well, it can lead to significant benefits for businesses and consumers alike.
Understanding the Components of a Supply Chain
Supply chain is a complex network of interconnected parts working in harmony. Understanding these components is important for any business looking to optimize its operations. Here are the key components:
- Suppliers. Provide the raw materials or components needed to create a product or service. They are the starting point of the supply chain and ensure the quality and availability of the necessary inputs.
- Manufacturers. Producers take the raw materials supplied and convert them into finished products. This process can involve a single company or a network of manufacturers, each specializing in different stages of production.
- Warehouses. Store both raw materials and finished goods before they are needed in the production process or delivered to customers. Effective management ensures that goods are preserved in optimal conditions and are readily available when required.
- Distribution centers. Serve as hubs that receive products from multiple manufacturers and then sort, repackage, and distribute them to retailers or directly to customers. They are essential for managing inventory levels and ensuring timely delivery.
- Retailers. Final link in the supply chain before the product reaches the consumer. They purchase products from manufacturers or distributors and sell them to the end user. Retailers can be brick-and-mortar stores, online platforms, or a combination of both.
- Transportation. Transportation is the connective tissue of the supply chain, encompassing all the logistics involved in moving goods from one location to another. This includes a variety of modes such as shipping, rail, air, and trucking.
- Information Technologies. Provide the data and analytics necessary to make informed decisions, track products, manage inventory, and streamline operations.
- Consumers. The end-users of the product and the driving force behind the supply chain. Their demand dictates the flow of goods and services through the supply chain.
- Return / Recycling Systems. These are often-overlooked components. They include the processes for handling returns, exchanges, and the recycling of materials, which is increasingly important for sustainability.
By understanding these components, businesses can identify areas for improvement and create a supply chain that meets current demands and is agile enough to adapt to future challenges.
Sourcing and Procurement
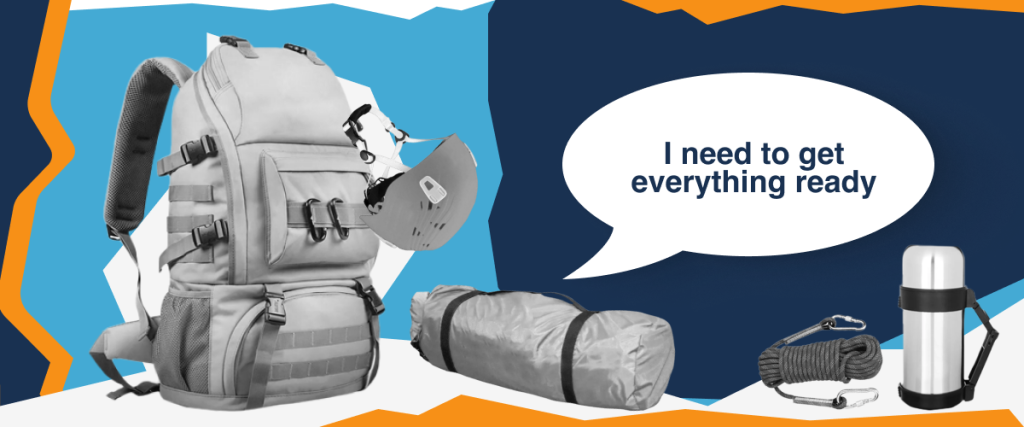
Sourcing is the process of identifying and selecting suppliers that can provide the goods and services a company needs to create its products. It's a strategic effort that goes beyond mere price negotiation. Effective sourcing involves a deep analysis of the supplier market, considering factors such as quality, reliability, technological capabilities, and the supplier's financial stability. The goal is to build partnerships that can yield mutual benefits and drive value creation for both parties.
Procurement is the operational process of acquiring the goods and services sourced from suppliers. It includes the transactional activities of purchasing but also includes the strategic aspects of managing supplier relationships and contracts. Acquisition teams work to ensure that the terms negotiated during sourcing are effectively implemented and that suppliers meet their commitments regarding quality, quantity, and timelines.
Sourcing and procurement play a huge role in managing risk within the supply chain. By thoroughly vetting suppliers and establishing robust contracts, these functions help mitigate the risks associated with supplier failure, geopolitical issues, and market volatility. Additionally, they ensure compliance with regulatory requirements and ethical standards, which is crucial in maintaining a company's reputation and avoiding legal penalties.
Supplier selection
This process involves evaluating and choosing suppliers for goods and services. Choosing the right one can significantly impact the quality, cost, and reliability of the final product. Here are some key considerations in the selection:
- Quality. Suppliers must meet the standards required for the products or services. This includes the materials used, the manufacturing processes, and the end product's performance.
- Cost. While cost should not be the only factor, it is important to consider the supplier's pricing to maintain profitability. This includes the unit cost and the total cost of ownership, which covers delivery fees, payment terms, and other related expenses.
- Reliability. Suppliers should have a track record of delivering goods and services on time and in the correct quantities. Reliability also refers to the ability to respond to changes in demand and maintain consistent supply.
- Communication. Effective communication channels between the buyer and supplier are essential for managing orders, addressing issues, and making adjustments as needed.
- Financial Stability. A supplier's financial health can affect their ability to deliver products and services consistently.
- Ethical Practices. Suppliers should adhere to ethical standards, including labor practices, environmental policies, and anti-corruption measures.
- Innovation. Suppliers that invest in research and development can offer innovative solutions that may provide a competitive edge.
- Geographical Location. The location of the supplier can affect shipping times and costs, as well as the ability to respond to emergencies.
- Flexibility. The ability of a supplier to adapt to changes in the business environment, such as scaling production up or down, is an important consideration.
- Risk Management. Assessing the risks associated with a supplier, including political, economic, and natural risks, is crucial for a resilient supply chain.
Contract negotiation
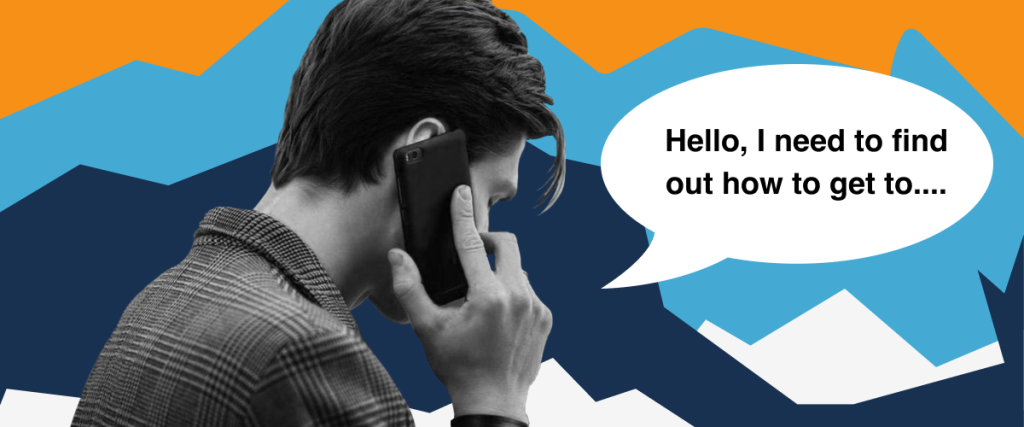
Contract negotiation in the supply chain is a step that involves reaching an agreement between two parties, typically the buyer and the supplier, on the terms of a contract that will govern their business relationship. Here are some aspects:
- Price terms. Negotiating the best possible price while ensuring quality and timely delivery is important. This includes discounts, payment terms, and volume commitments.
- Quality specifications. Clearly defining the quality requirements for the products or services to ensure they meet the company's standards.
- Delivery schedules. Establishing realistic delivery timelines that align with the production schedules and inventory needs.
- Risk allocation. Determining who bears the risk for various scenarios, such as delays, quality issues, or force majeure events.
- Liability and indemnity. Agreeing on the liability clauses for non-performance or breaches of contract, and indemnity for losses incurred.
- Intellectual property rights. Ensuring that intellectual property rights are protected and clearly defined within the contract.
- Confidentiality. Including confidentiality agreements to protect sensitive business information.
- Dispute resolution. Setting out the mechanisms for resolving disputes, including arbitration or litigation procedures.
- Termination clauses. Defining the conditions under which the contract can be terminated by either party.
- Renewal and modification. Outlining the terms for contract renewal and the process for making modifications to the contract.
Effective contract negotiation requires preparation, clear communication, and sometimes compromise. It's important to understand the needs and constraints of both parties and to build a relationship that can lead to long-term collaboration. The goal is to create a partnership that is fair, transparent, and provides a solid foundation for a successful business collaboration.
The specifics of contract negotiation can vary greatly depending on the industry, the size of the companies involved, and the nature of the goods or services being procured. It's often advisable to involve legal counsel to ensure that all contractual terms are legally sound and enforceable.
Manufacturing and Production
Once the raw materials are in hand, the manufacturing entity begins the transformation of these inputs into a finished product. The production workflow is tailored to align with market needs, fulfilling orders from distributors, wholesalers, and retailers within the limits of the manufacturer's operational capabilities. Typically, these capabilities hinge on the company's infrastructure, encompassing the scale of its facilities, the workforce employed therein, and the technological assets utilized.
Production planning
Production planning ensures that manufacturing operations are aligned with demand and resources are utilized efficiently. Here are some key points about its role:
- Demand forecasting. Production planning starts with predicting demand to determine how much product needs to be produced to meet customer requirements.
- Resource allocation. It involves allocating the necessary resources, including materials, labor, and equipment, to meet production targets.
- Scheduling. Detailed schedules are created for when each task in the production process should start and finish to ensure timely completion of products.
- Inventory management. Production planning is closely tied to inventory management, ensuring that there is enough raw material to produce goods without overstocking and incurring unnecessary costs.
- Cost control. By planning production in advance, companies can control expenses more effectively, avoiding rush orders and overtime costs.
- Quality management. It ensures that the production process adheres to quality standards, reducing waste and rework.
- Flexibility. Well planning allows for agility to adapt to changes in demand or production issues.
- Coordination with other departments: Production planning requires collaboration with procurement, logistics, and sales to ensure a smooth flow of materials and finished goods through the supply chain.
- Continuous improvement. Production planning is not a one-time task. It involves continuous analysis and improvement of processes to increase efficiency and reduce costs.
In essence, production planning is about making the right product, in the right quantity, at the right time, and at the right cost, which is essential for the success of any manufacturing operation within the supply chain.
Quality control
Quality control ensures products meet standards and specifications. It involves systematic processes for detecting defects and nonconformities, allowing for corrective actions to be taken before products reach the customer.
Effective quality control helps maintain product integrity, reduces costs associated with returns and repairs, and enhances customer satisfaction. It requires collaboration across various stages of the supply chain, from sourcing raw materials to the manufacturing processes, and finally to the delivery of the finished goods. By implementing rigorous quality control measures, companies can build a reputation for reliability and excellence, which is vital in today's competitive market.
Logistics and Transportation
Logistics and transportation ensure the smooth flow of goods from suppliers to customers. This segment involves a variety of activities, from managing inventory to selecting the most efficient delivery routes. The major aspects of this process include:
- Inventory management. Keeping track of stock levels to meet demand without overstocking.
- Transportation mode selection. Choosing the most appropriate method of transport, such as air, sea, rail, or road, based on cost, speed, and product type.
- Route optimization. Planning the most efficient paths to minimize delivery times and fuel consumption.
- Carrier management. Working with shipping companies to secure reliable and cost-effective transportation services.
- Compliance and regulations. Adhering to international and local laws governing the movement of goods.
Effective logistics and transportation strategies can significantly reduce costs, enhance customer satisfaction, and improve the overall performance of the supply chain.
Inventory management
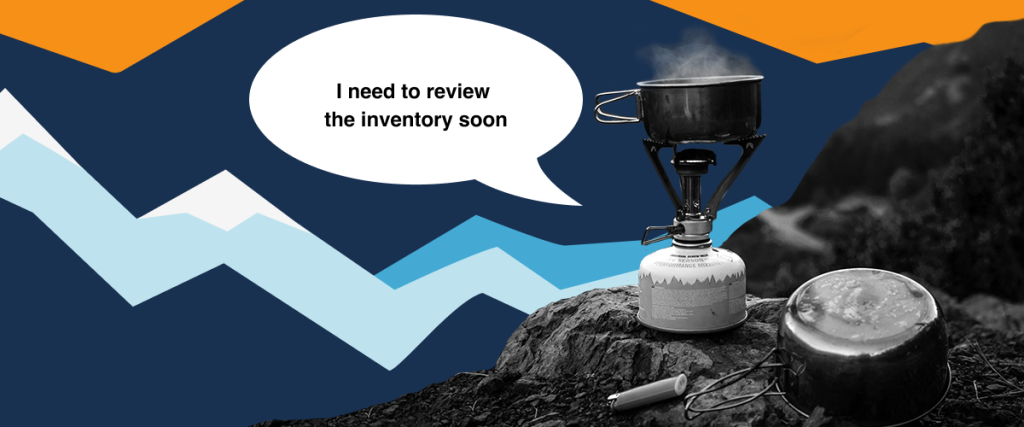
Inventory Management involves overseeing and controlling the ordering, storage, and use of components that a company will use in the production of the items it will sell. It also includes the management of finished products that are ready for sale.
It is important to Maintain Optimal Inventory Levels to ensure that the production process is uninterrupted and customer demand is consistently met without excessive surplus. By minimizing the amount of inventory held, companies can reduce storage costs and the risk of inventory obsolescence. Efficient inventory management can free up capital that would otherwise be tied up in stock. By having the right products available at the right time, businesses can improve service levels and customer satisfaction.
Effective inventory management strategies often employ various tools and techniques, such as just-in-time (JIT) inventory systems, economic order quantity models, ABC analysis, and inventory management software, to streamline operations and align inventory levels with production and sales demands.
Distribution networks
Distribution networks in the supply chain are the interconnected systems that facilitate the transfer of products from the manufacturer to the end consumer. These networks encompass various intermediary steps, including warehouses, distribution centers, and retail outlets. Key functions of distribution networks include:
- Consolidation. Gathering small product shipments and combining them into larger, more economical loads.
- Cross-Docking. Minimizing storage time by directly transferring products from incoming to outgoing trucks.
- Order fulfillment. Processing customer orders efficiently to ensure accurate and prompt delivery.
- Reverse logistics. Handling returns and exchanges in a way that maximizes value recovery.
An optimized distribution network reduces transit times, lowers costs, and improves service levels, ultimately contributing to a competitive advantage in the marketplace. Effective management of these networks is crucial for maintaining the balance between supply and demand, ensuring product availability, and achieving customer satisfaction.
Warehousing and Inventory Management
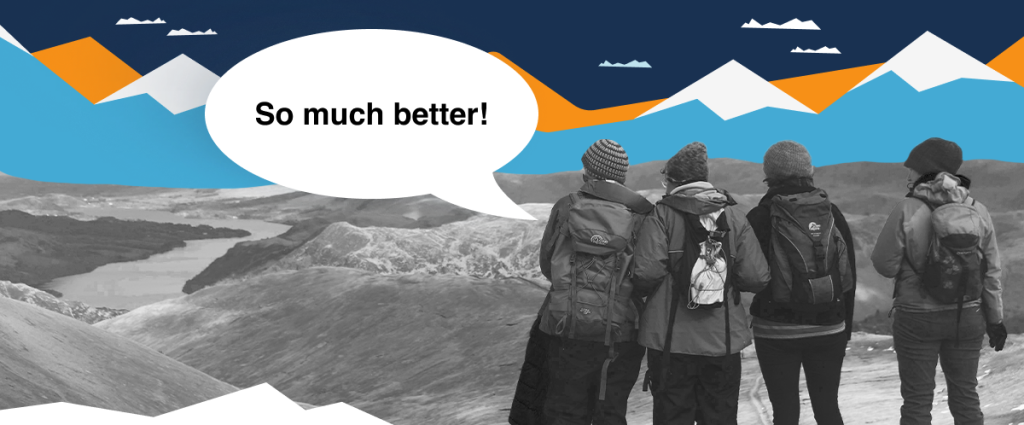
Warehousing and inventory management ensure that products are stored, managed, and distributed efficiently to meet market demand. Effective warehousing provides safe and secure storage for a diverse range of goods, optimizing space utilization and facilitating quick turnover. Meanwhile, robust inventory management systems track stock levels in real-time, enabling precise forecasting, reducing waste, and ensuring that the right products are available at the right time. Together, these elements support a resilient supply chain that can adapt to changing consumer needs and market conditions.
Storage Facilities
They are designed to accommodate goods in a variety of environments tailored to the products' needs, such as temperature-controlled spaces for perishable items or high-security areas for valuable goods. Strategic location of these facilities plays a crucial role in minimizing transportation costs and delivery times. Modern warehouses are also adopting green practices, such as solar panels and energy-efficient lighting, to reduce environmental impact.
Inventory Tracking Systems
Customer Service and Satisfaction
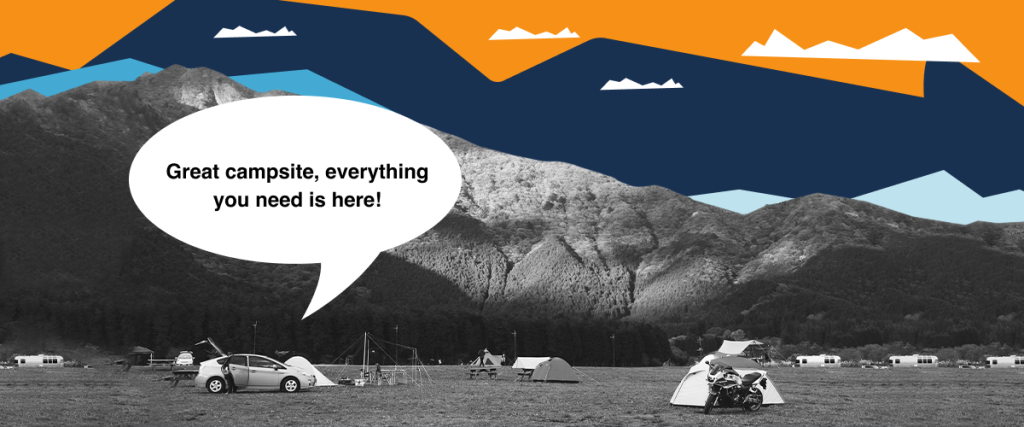
The main point of any successful supply chain is the level of customer service and satisfaction it delivers. In today's competitive market, these elements are not just add-ons but central to a company's value proposition. Below, we delve into two important aspects that significantly impact customer perceptions and business success.
Order Fulfillment
Order fulfillment is the critical bridge between sales and customer satisfaction. It encompasses the entire process from sale to delivery, ensuring that customers receive their products promptly and accurately. This stage requires a seamless integration of inventory management, warehousing, and logistics to minimize delays and errors. By optimizing order fulfillment, companies can not only meet but exceed customer expectations, fostering loyalty and encouraging repeat business.
After-sales Support
After-sales support represents the ongoing relationship with the customer following the initial purchase. It includes customer service, warranty management, returns, repairs, and maintenance services. Effective after-sales support can transform a one-time buyer into a lifelong customer. It's an opportunity to demonstrate commitment to quality and service excellence, providing assistance and resolving any issues swiftly to maintain customer trust and satisfaction.
Customer service and satisfaction are the end goals of a well-managed supply chain. By focusing on efficient order fulfillment and robust after-sales support, businesses can ensure a positive customer experience that leads to sustained growth and a strong market presence.
The Role of Information and Technology in SCM
In the intricate web of SCM, information and technology streamline operations, enhance transparency, and foster informed decision-making. The integration of advanced technologies has not only revolutionized SCM but also equipped it to face the dynamic demands of the modern market.
Data-driven Decision Making
Data-driven decision making empowers businesses to analyze historical data, assess current market trends, and make strategic decisions that align with their operational goals. By leveraging real-time data, companies can optimize inventory levels, improve procurement processes, and reduce operational costs.
Supply Chain Analytics
Supply chain analytics provide a particular view of the supply chain operations, offering insights into every facet from procurement to product delivery. These analytics help in identifying inefficiencies, predicting potential disruptions, and suggesting actionable strategies to mitigate risks and enhance performance.
Predictive Modeling
Predictive modeling uses statistical techniques and machine learning algorithms to forecast future events based on historical data. In SCM, this translates to anticipating demand fluctuations, supply chain bottlenecks, and even predicting maintenance requirements for logistics infrastructure.
Technology Adoption
Staying competitive in today's market requires embracing new technologies — it's a necessity, not an option.
ERP systems are comprehensive software platforms that integrate all facets of a business's operations, including SCM. They provide a unified source of truth for data across departments, facilitating better coordination and planning.
Dedicated SCM software goes a step further by focusing on optimizing the supply chain's specific needs. These solutions offer tools for everything from warehouse management to transportation logistics, ensuring that every link in the supply chain is strong and responsive.
By harnessing the power of information and technology, SCM can achieve unprecedented levels of efficiency and agility, positioning businesses to thrive in an ever-evolving economic landscape.
Collaboration and Coordination Across the Supply Chain
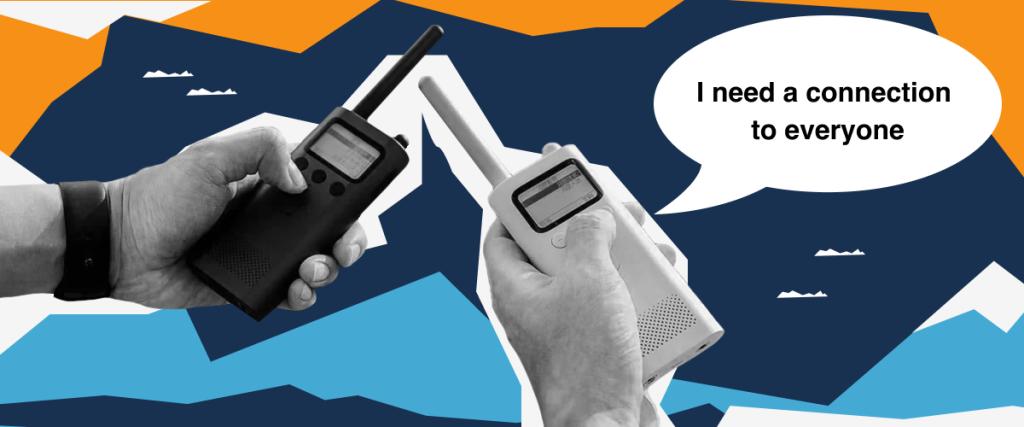
Effective SCM requires collaboration and coordination among all stakeholders involved in the supply chain, including suppliers, manufacturers, distributors, retailers, and customers. Collaboration enables real-time information sharing, demand forecasting, and inventory management, leading to improved efficiency and responsiveness to market demands.
Supplier Relationships
A strategic approach to supplier management involves selecting reliable suppliers, negotiating favorable terms, and fostering open communication channels. By working closely with suppliers, organizations can mitigate risks, optimize costs, and enhance product quality and innovation.
Collaborative partnerships
Collaborative partnerships go beyond traditional buyer-supplier relationships and involve sharing risks, rewards, and resources to achieve mutual benefits. These often entail joint product development, sharing of market insights, and co-investment in technology and infrastructure. Collaborative efforts foster innovation, agility, and competitive advantage in the supply chain.
Vendor management
Vendor management focuses on overseeing the performance of suppliers and ensuring they meet the organization's requirements and standards. It involves a systematic approach to selecting, monitoring, and optimizing relationships with vendors to achieve strategic objectives and drive value throughout the supply chain.
Integration with Partners
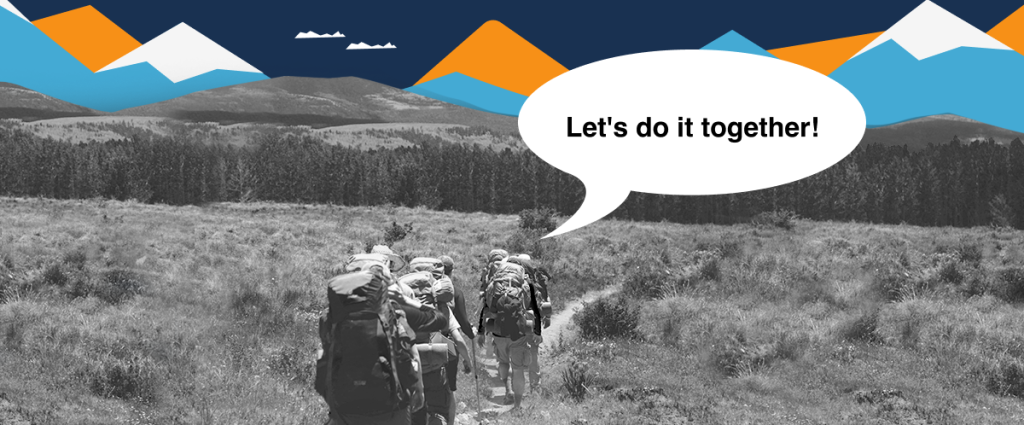
Integration with partners involves connecting and aligning systems, processes, and workflows across the supply chain to facilitate seamless collaboration and coordination. This integration enables real-time data sharing, enhances visibility, and improves efficiency and responsiveness to changes in demand and market conditions.
Interconnected systems
Interconnected systems refer to the integration of various software applications, databases, and technologies used by different stakeholders across the supply chain. Here's a deeper dive into interconnected systems in SCM:
- Enterprise Resource Planning (ERP) Systems. ERP systems provide a centralized platform for managing core business processes such as procurement, production, inventory management, order fulfillment, and financials. By integrating modules for different functional areas, ERP systems enable real-time visibility into operations and facilitate data-driven decision-making.
- Warehouse Management Systems (WMS). WMS software optimizes warehouse operations by automating tasks such as receiving, put-away, picking, packing, and shipping. Interconnected WMS systems integrate with ERP and other SCM systems to exchange data on inventory levels, order status, and shipment tracking in real-time, ensuring accurate inventory management and efficient warehouse operations.
- Transportation Management Systems (TMS). TMS software streamlines transportation planning, execution, and optimization processes, including route planning, carrier selection, freight booking, and shipment tracking. Interconnected TMS systems integrate with ERP, WMS, and external logistics partners to exchange data on orders, shipments, and transportation costs, enabling better coordination and visibility across the supply chain.
- Supplier Relationship Management (SRM) Systems. SRM systems facilitate the management of supplier relationships, contracts, and performance metrics. Interconnected SRM systems enable organizations to collaborate with suppliers on order processing, delivery schedules, quality control, and supplier evaluations, fostering transparency and accountability in supplier relationships.
- Customer Relationship Management (CRM) Systems. CRM systems manage customer interactions and sales processes, including lead management, opportunity tracking, and customer service. Interconnected CRM systems integrate with ERP and order management systems to provide a unified view of customer data, orders, and service history, enabling personalized marketing, sales, and support experiences.
- Electronic Data Interchange (EDI) Platforms. EDI platforms enable the electronic exchange of business documents, such as purchase orders, invoices, and shipping notices, between trading partners. Interconnected EDI systems facilitate seamless communication and data integration between internal and external systems, reducing manual data entry and errors in transaction processing.
- Collaboration Platforms. Collaboration platforms, such as cloud-based portals or supplier portals, facilitate communication and collaboration among supply chain partners. Interconnected collaboration platforms enable stakeholders to share documents, track progress, and collaborate on projects in real-time, improving efficiency and decision-making.
Communication channels
Communication channels in Supply Chain Management (SCM) are the various methods and platforms used by stakeholders to exchange information, coordinate activities, and collaborate effectively throughout the supply chain. Effective communication channels are essential for ensuring timely decision-making, resolving issues, and maintaining alignment among supply chain partners.
The most popular communication channels in SCM are:
- Phone Calls
- Video Conferencing
- Collaboration Platforms
- Supplier Portals
- EDI (Electronic Data Interchange)
- Social Media
- Webinars and Online Training
Key Processes and Strategies in Supply Chain Management
There are a number of important processes and strategies in SCM. They are essential for creating a resilient and responsive supply network.
Demand forecasting is a critical strategy that involves using historical data and predictive analytics to anticipate customer demand, allowing companies to align their production schedules and inventory levels accordingly. Inventory optimization ensures that a company maintains the optimal stock levels to meet demand without incurring excess costs or storage issues. Supply chain risk management is about identifying potential disruptions in the supply chain, from natural disasters to supplier insolvency, and developing contingency plans to mitigate these risks.
Together, these strategies empower businesses to maintain continuity, maximize efficiency, and drive competitive advantage in the marketplace.
Demand forecasting
Effective demand forecasting involves several steps:
- Data Collection. Gathering historical sales data, market trends, and other relevant information.
- Analysis. Using statistical tools and algorithms to analyze the data and identify patterns.
- Predictive Modeling. Developing models that can predict future demand based on the analyzed data.
- Continuous Improvement. Regularly updating models with new data and adjusting strategies as market conditions change.
The goal is to align supply with predicted demand as closely as possible, minimizing stockouts and overstock situations. This not only ensures product availability but also contributes to a lean and cost-effective supply chain. Demand forecasting is not without challenges, however, as it must account for various uncertainties and complexities of the market. Therefore, it's a dynamic and ongoing effort that requires constant refinement and adaptation.
Predictive analytics
Predictive analytics is a forward-looking approach that utilizes data, statistical algorithms, and machine learning techniques to identify the likelihood of future outcomes based on historical data. It's about understanding the patterns in data to anticipate future supply chain disruptions, demand spikes, or inventory shortages.
By analyzing trends and patterns, businesses can proactively adjust their strategies for sourcing, inventory management, and distribution. For example, predictive analytics can forecast consumer demand for products accurately, allowing companies to optimize their inventory levels and reduce holding costs. It can also highlight potential supply chain risks, such as delays from suppliers or changes in market conditions, enabling companies to take preemptive action to mitigate these risks.
In essence, predictive analytics provides a significant competitive edge by transforming data into actionable insights, leading to more informed decision-making, improved operational efficiency, and enhanced customer satisfaction.
Demand planning techniques
- Historical Data Analysis. This involves examining past sales data to identify trends and patterns that can predict future demand. It's the foundation for most forecasting models.
- Statistical Forecasting. Techniques such as time series analysis, regression analysis, and econometric modeling are used to predict future demand based on quantitative data.
- Market Analysis. Keeping a close eye on market trends, economic indicators, and consumer behavior helps in adjusting demand forecasts to align with current market conditions.
- Collaborative Planning. Working with suppliers, customers, and other partners to share information and insights can lead to more accurate demand predictions.
- Machine Learning and AI. Advanced algorithms can analyze large datasets to uncover complex patterns and improve forecast accuracy over time.
- Scenario Planning. Developing multiple 'what-if' scenarios to understand the potential impact of various factors on demand, such as new product launches or changes in the competitive landscape.
- Sales and Operations Planning (S&OP). Integrating sales forecasts with operational plans ensures that the supply chain is prepared to meet demand while maintaining efficiency.
By employing these techniques, businesses can create more accurate demand forecasts, which are crucial for reducing inventory costs, improving customer satisfaction, and enhancing overall supply chain performance.
Inventory Optimization
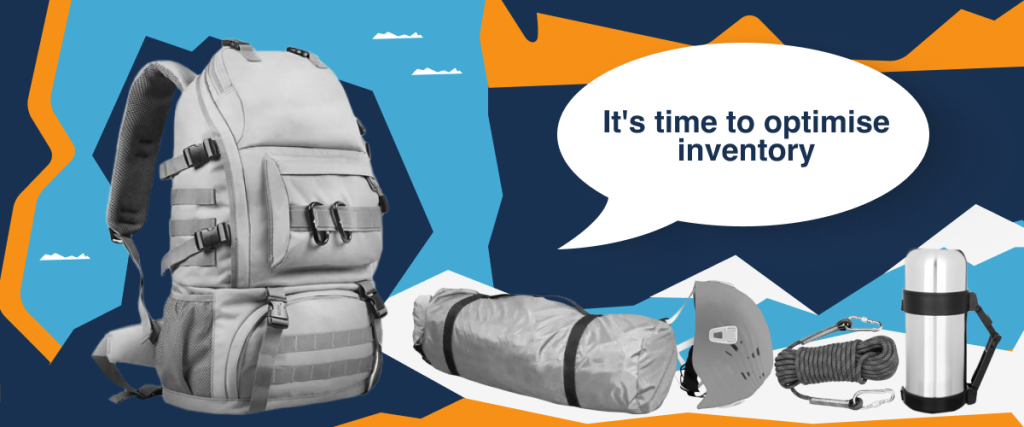
Inventory Optimization aims to maintain the ideal balance between the inventory investment and service levels provided to customers. It involves a series of strategies and tools that help in determining the optimal quantity and timing of inventory. These strategies include:
- Just-In-Time (JIT). This strategy focuses on reducing inventory levels by aligning order times with production schedules and customer demand, minimizing the holding costs of inventory.
- Safety Stock Management. By keeping a calculated amount of extra stock to prevent stockouts caused by unforeseen fluctuations in demand or supply delays, businesses can ensure a steady supply.
- ABC Analysis. This categorization method prioritizes inventory based on the significance of different items and helps manage inventory more effectively by focusing on the most impactful items.
- Economic Order Quantity (EOQ). EOQ is a formula used to determine the most cost-effective quantity to order, balancing the costs of ordering and holding inventory.
Just-in-Time (JIT) inventory
Just-in-Time (JIT) inventory is a management strategy that aligns raw-material orders from suppliers directly with production schedules. It is used in Supply Chain Management (SCM) to increase efficiency and decrease waste by receiving goods only as they are needed in the production process, thereby reducing inventory costs. This method requires producers to forecast demand accurately and streamline their production processes to ensure quick turnaround times and reduce lead times.
The JIT approach differs significantly from traditional inventory systems, where large quantities of materials are ordered to take advantage of quantity discounts and held in stock, resulting in higher inventory holding costs. Instead, JIT focuses on continuous improvement and responding flexibly to changing customer demands. By reducing inventory levels, companies can minimize the costs associated with excess inventory, such as storage, spoilage, and insurance.
However, JIT also comes with risks, particularly in the form of supply chain disruptions. If a supplier fails to deliver materials on time, it can halt the entire production process. Therefore, while JIT can lead to significant cost savings and efficiency improvements, it requires a stable supply chain and excellent coordination with suppliers. Companies using JIT will often invest in supply chain risk management strategies to mitigate these risks and ensure a smooth production flow.
Inventory turnover ratios
Inventory turnover ratio measures the efficiency of a company in managing and selling its inventory over a certain period. It is calculated by dividing the cost of goods sold (COGS) by the average inventory during the same timeframe. The formula is expressed as:
Inventory Turnover = (Cost of Goods Sold / Average Inventory)
A higher inventory turnover indicates that a company is selling goods rapidly and suggests efficient inventory management. Conversely, a low turnover may imply overstocking, which can tie up capital and increase storage costs.
By monitoring this ratio, businesses can gain insights into their product demand, sales effectiveness, and inventory management practices, enabling them to make informed decisions on purchasing and production, ultimately leading to a more streamlined and cost-effective supply chain.
Supply Chain Risk Management
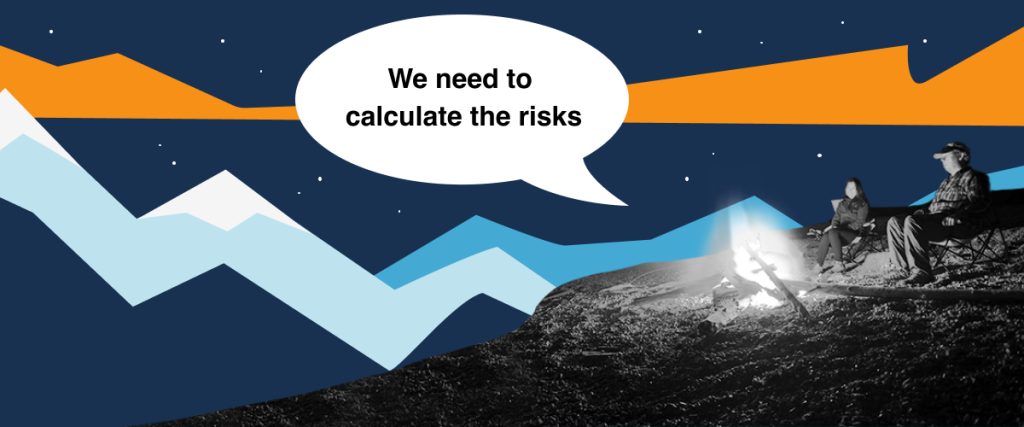
Supply chain risk management (SCRM) is the beacon that guides companies through tumultuous waters. It's a strategic approach that identifies, assesses, and mitigates risks within the supply chain to ensure business continuity and reliability.
Identifying and Mitigating Risks
The first step in SCRM is to identify potential risks that could disrupt the supply chain. These risks can range from geopolitical instability and regulatory changes to natural disasters and cyber-attacks. Once identified, the next step is to assess the likelihood and impact of these risks. This assessment helps prioritize the risks and develop strategies to mitigate them.
Mitigation strategies may include diversifying suppliers, investing in cybersecurity, or developing alternative logistics routes. The goal is to reduce both the probability of risk occurrence and its potential impact on the supply chain.
Contingency Planning
Contingency planning is about being prepared for when things go wrong. It involves creating plans for quick response and recovery in case of a supply chain disruption. This includes establishing emergency procedures, setting up backup systems, and training employees to handle crises.
Effective contingency planning ensures that a company can maintain operations or resume them as quickly as possible after a disruption. It's about having a plan B, C, and even D, ensuring that the supply chain is resilient in the face of challenges.
By identifying and mitigating risks and having robust contingency plans in place, companies can protect themselves against the unexpected and maintain a competitive edge in the market.
Examples and Case Studies
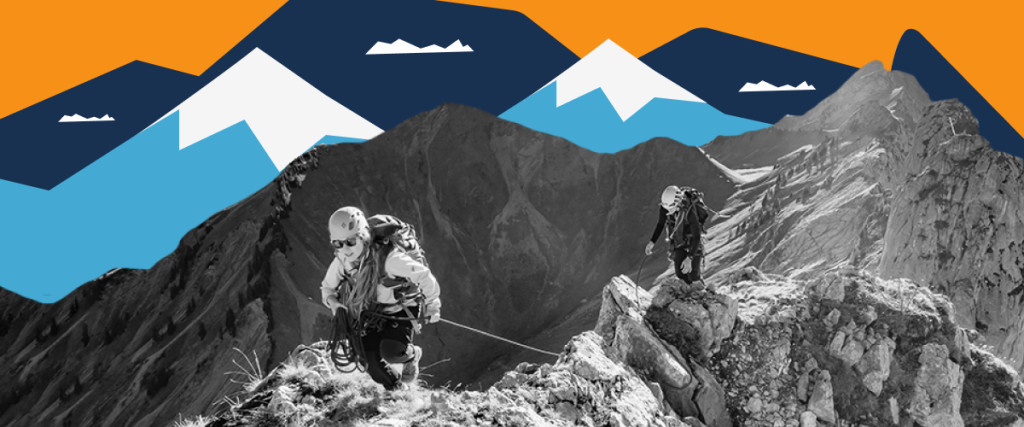
TeamIdea has various examples and cases that exemplify the significance of SCM in ensuring the smooth flow of materials, information, and finances across the supply chain. Here are some of our notable examples and cases of supply chain management optimization with SAP tools.
Sberlogistics
Sberlogistics – one of the largest logistics operators in CIS with 5 class A warehouses exceeding 130 000 m2, 82 regional centers, 2 500 pick-up points, and 10 500 parcel terminals. For Sberlogistics TeamIdea has implemented a unique solution based on SAP Extended Warehouse Management.
Project goals: to unite all the warehouse activities of Sberlogistics in a single automated system
Project Features:
- Providing warehouse logistics for SberMegaMarket – an e-Commerce platform and mobile app for consumer goods.
- 9 food warehouses for Samokat – e-grocery service, dark store rapid delivery service for food and household goods.
Results: 99,9% picking service level, 80.000-100.000 order lines picked daily, flexible delivery pricing implementation for 10.000.000+ SKUs.
Exist
Exist – the largest online auto parts store in CIS Russia, the project of a robotic distribution center with Beumer sorting equipment and Schaffer conveyors, 20 million SKU. SAP ERP / EWM on Hana solution was implemented using the Material Flow System module.
Project Goals:
- Increase warehouse productivity at least twice, but as a maximum three times;
- Reduction of the cost of cargo handling, flexible pricing depending on costs;
- Increase in own share of goods up to 50% in total sales;
- Implementation of industrial warehouse management system, scalability, performance.
Results: all the KPIs achieved, the warehouse for 1700 sq meters is fully managed by a single automated system. During the project our team has accumulated unique experience in integration with automated equipment.
MARS
MARS — US FMCG company. Main brands – Mars, Snickers, Milky Way, Twix, Bounty, M&M’s, Pedigree, Uncle Ben’s. TeamIdea automated 8 factories for MARS using a solution pre-built on SAP EWM.
Project Goals: to replace an outdated warehouse system in the biggest MARS Distribution center in CIS (Sitenka DC) and significantly reduce the risk of stopping shipments to customers and production halts in one of the factories.
SAP EWM solution template was designed for all 8 factories, taking into account the warehouse topology and specific.
Wave 1: implementation at 7 factories (including scalable system landscape creation, basic processes and integrations): 4 Pet Food factories, 2 Chocolate factories and 1 Food-factory.
Wave 2: rollout to the Sitenka DC and adoption to its processes.
Project results:
- SAP EWM template for 8 factories in CIS region.
- Quality control management, including full traceability for each batch.
- Agile implementation methodology. As a result – high customer satisfaction with the final product.
- Seamless integration: no business impact during go-live and minimum downtime.
These examples and cases demonstrate the diverse ways in which effective supply chain management practices can drive operational excellence, customer satisfaction, and competitive advantage in various industries.
Future Trends and Innovations in Supply Chain Management
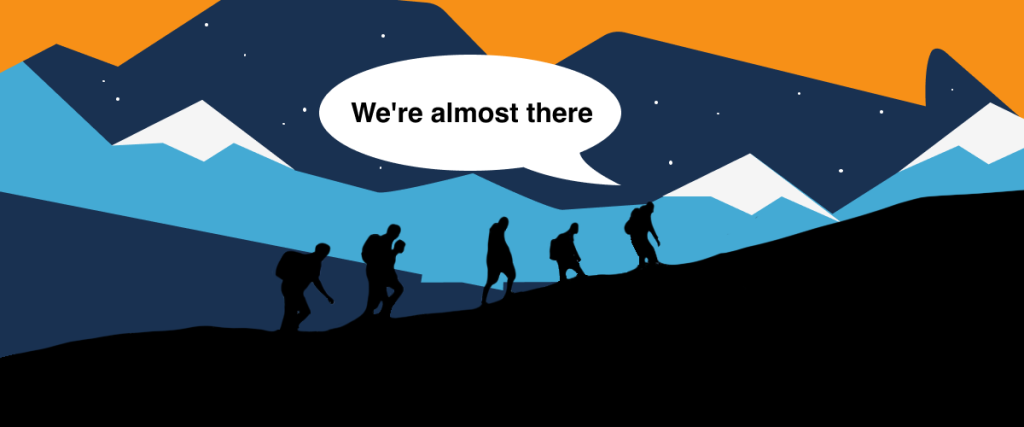
The landscape of Supply Chain Management (SCM) is continuously evolving, shaped by the forces of technological advancement and a growing consciousness of sustainability and ethics. As we look to the future, several key trends and innovations are poised to redefine SCM practices.
Sustainability and Ethical Sourcing
In the realm of global trade and industry, sustainability and ethical sourcing stand as twin pillars supporting the long-term health of our planet and its inhabitants. These concepts are not just moral choices but strategic imperatives that can define a company's legacy and its future.
Green Supply Chains
The push towards green supply chains is a response to the urgent need for environmental stewardship. Companies are re-evaluating their operations to reduce carbon footprints, minimize waste, and promote recycling. This includes optimizing logistics to lower emissions, sourcing materials responsibly, and embracing circular economy principles.
Fair Trade Practices
Fair trade practices are gaining traction as consumers increasingly demand transparency and ethical treatment of workers. Companies are focusing on fair labor practices, equitable pay, and sustainable sourcing. This ethical shift not only benefits the workforce and the environment but also enhances brand reputation and customer loyalty.
Emerging Technologies
The advent of new technologies has always been a catalyst for change in supply chain management. As we advance, several emerging technologies stand out for their potential to transform the industry, e.g. AI, Internet of Things, Blockchain, Robotics and Automation.
Blockchain
Blockchain is emerging as a foundational technology for enhancing transparency and security in supply chains. Its decentralized nature allows for a tamper-proof ledger of transactions, offering a new level of trust and collaboration among supply chain partners. Key benefits include:
- Immutable record-keeping, which ensures that once data is entered into the blockchain, it cannot be altered, providing a single source of truth.
- Enhanced traceability, allowing for the tracking of products from origin to consumer, ensuring authenticity and compliance with regulations.
- Smart contracts, which automate transactions and enforce agreements between parties, streamlining operations and reducing the potential for disputes.
Internet of Things (IoT)
The Internet of Things (IoT) is revolutionizing SCM by connecting physical objects to the internet, enabling them to send and receive data. This brings a new level of intelligence to supply chains, with applications such as:
- Real-time tracking of goods, providing visibility into the location and condition of products throughout the supply chain.
- Predictive analytics, using data from sensors to forecast demand, manage inventory levels, and optimize routing.
- Maintenance alerts, where IoT devices can predict equipment failures before they occur, reducing downtime and maintenance costs.
These emerging technologies are not just shaping the future of supply chain management; they are actively constructing it. By harnessing blockchain and IoT businesses can create more resilient, responsive, and efficient supply chains, ready to meet the challenges of a rapidly changing world.
Conclusion
Recap of key points
- SCM integrates supply and demand management within and across companies to deliver the highest value to customers at the lowest cost to the supply chain as a whole.
- One of the most important steps in SCM is to identify potential risks that could disrupt the supply chain. These risks can range from geopolitical instability and regulatory changes to natural disasters and cyber-attacks.
- SCM optimizes the production and distribution process, which can significantly reduce costs. This includes minimizing waste, and improving procurement processes.
- Nowadays SCM is focused on mitigating environmental impacts and addressing ethical issues.
- The development of SCM is tied to the development of new advanced technologies such as AI, blockchain, Internet of Things, etc.
Importance of Effective Supply Chain Management for Businesses
Effective SCM is crucial for businesses as it directly impacts their ability to serve customers efficiently and maintain a competitive edge. It ensures that products are delivered on time, costs are controlled, and resources are utilized optimally. Moreover, it enables companies to respond swiftly to market changes and customer demands.
Final thoughts on the future direction of supply chain management
As businesses continue to navigate a rapidly evolving landscape, the integration of these technologies will be key to achieving long-term success and sustainability.
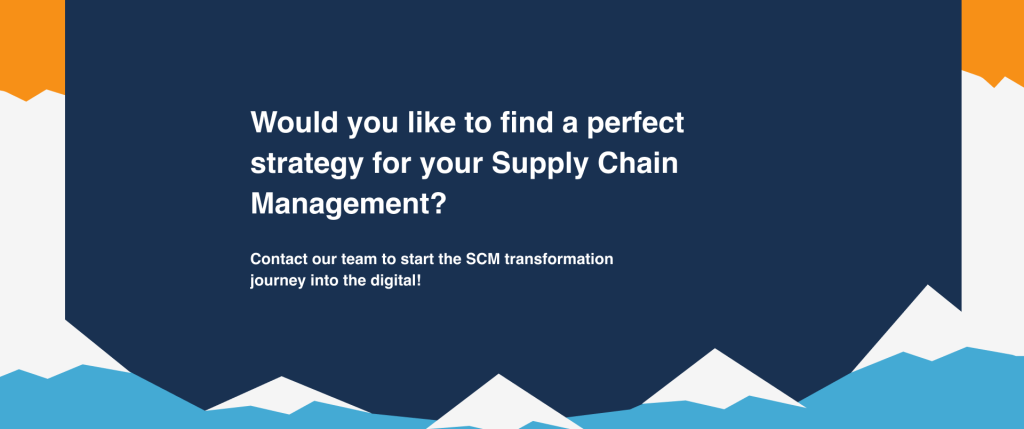
Key takeaways
-
Supply Chain Management (SCM)
Supply Chain Management involves managing the entire production flow of a good or service, from the acquisition of raw materials to the delivery of the final product to consumers. -
Why is SCM important for businesses?
SCM enhances efficiency, reduces operational costs, and improves customer satisfaction. Effective SCM helps manage risks, adapt to market changes, and ensures timely delivery of quality products. -
What strategies can businesses use to improve their SCM?
Businesses can improve their SCM by building strong supplier relationships, adopting lean principles to minimize waste, enhancing agility to quickly respond to changes, and investing in advanced technologies for better decision-making and efficiency. -
Sustainability in SCM
Sustainability in SCM involves adopting environmentally friendly practices, reducing waste, and ensuring ethical sourcing and production processes. It is increasingly important due to regulatory requirements and consumer demand for sustainable products. -
SCM for small businesses
Small businesses can benefit significantly from SCM by streamlining their operations, reducing costs, and positioning themselves better against competitors. Effective SCM helps small businesses operate more efficiently and scale their operations as they grow.