1443
7 min
Planning Challenges for Automotive Suppliers: How to Fulfill Orders in 2 Hours and Avoid Overstocks?

How do automotive manufacturers streamline their planning processes to handle such complexity? What role does automation play in improving efficiency and meeting JIT and JIS requirements? And how can advanced planning solutions help in making crucial production decisions?
Natalia Morozova, an IBP expert and architect at TeamIdea, shares her insights on these questions. Let's explore the different aspects of planning in the automotive sector and find out how to tackle these challenges with automation and advanced planning solutions.
Automotive industry specifics
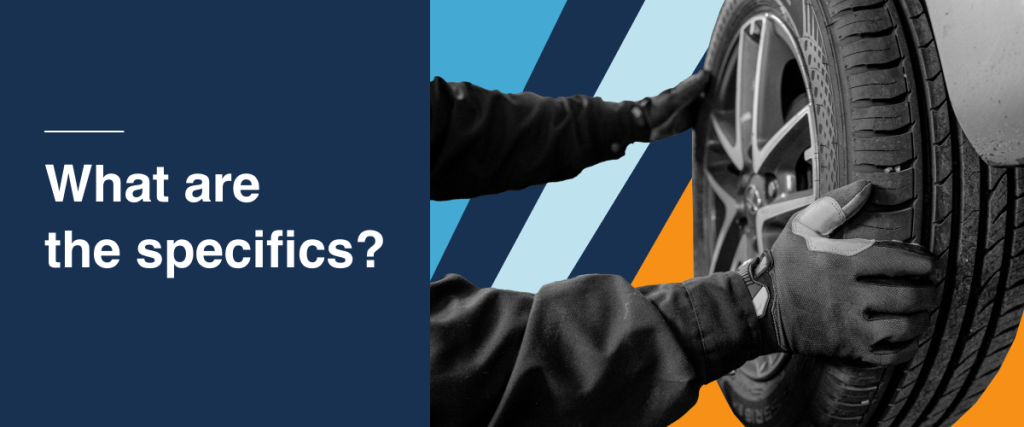
What you need to consider when talking about the automotive industry:
- Complexity of SKUs and production variants. The automotive components sector handles numerous SKUs, each with the characteristic variants such as different colors, models, and size.
- Manufacturers may opt to produce in-house or outsource production, balancing capacity needs and selecting the best partners for outsourcing decisions. Orders are often transmitted through Electronic Data Interchange (EDI), a special protocol for exchanging data between final assembly automotive companies and component producers / OEM (Original equipment manufacturer).
- High service levels and penalty costs. The industry demands high service levels due to Just-In-Time (JIT), and Just-In-Sequence (JIS) processes. Failure to deliver components in the correct sequence and quantity can halt the client's car final assembly line, leading to significant financial losses. Car manufacturers impose high penalty costs on suppliers for not fulfilling orders accurately and timely.
Challenges in planning in automotive manufacturing
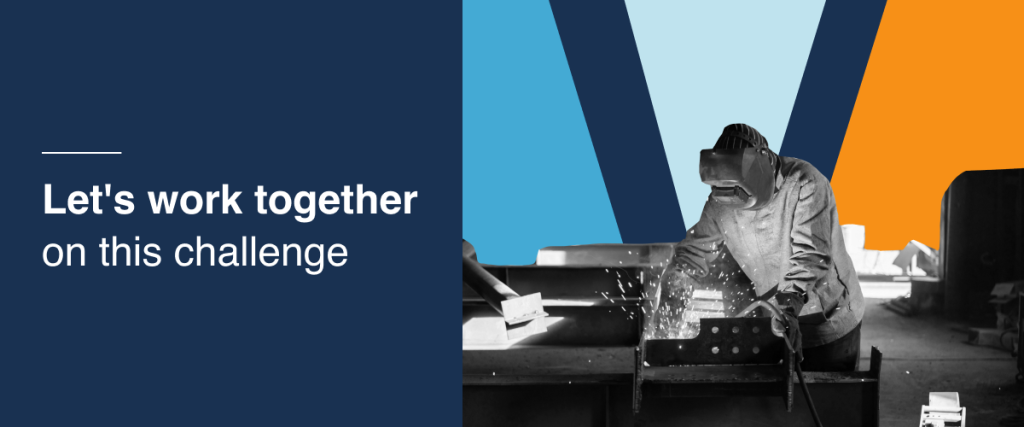
The biggest headache? Planning and managing a vast number of SKUs while hitting almost 100% service levels without drowning in surplus stock. High service level agreements often lead to overstock, tying up capital and cluttering operations.
Here are some challenges, faced by automotive manufacturers:
- Variety of SKUs and production variants. This complexity is driven by the need to cater to different market demands and preferences.
- Each variant may require different production processes. For instance, changing the color of a component involves adjusting the painting machinery, leading to production downtime and affecting planning.
- Phantom assemblies. Automotive manufacturers often use phantom assemblies — logical groupings of components that don't physically exist but are used for engineering purposes. This adds another layer of complexity to the planning process.
- Project-based work. Many automotive components manufacturers operate on a project basis, collaborating with car manufacturers to design, engineer, and produce specific components. These projects can span several years and involve extensive research, engineering, designing, testing and complying to safety regulations, adding challenges to the planning.
- Just-In-Time and Just-In-Sequence processes. This means automotive suppliers need to deliver components precisely when needed and in the correct sequence, matching the car final assembly line's order. This double complexity requires rapid and accurate planning and execution.
Addressing the challenges: a case of international automotive components producer
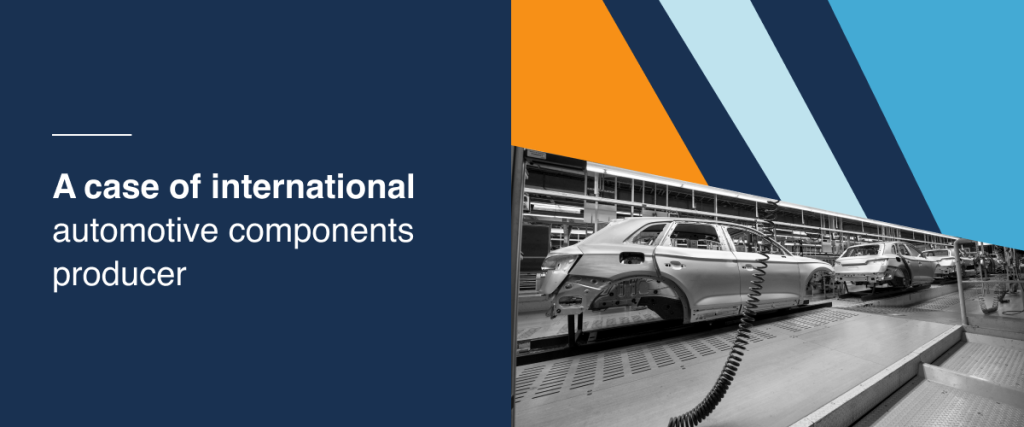
In a recent project with an international automotive components producer, we encountered and addressed several of these challenges.
Initial situation. Our client is a major international company operating in various regions, including Europe, MENA, and Asia, with over 30 plants and engineering centers worldwide. They supply well-known car brands such as Ford, Audi, Renault, and Toyota. When we began discussing their planning situation, they faced the following issues:
- Static safety stock calculation. They were calculating static safety stock in days of coverage, which was updated manually. This update process occurred infrequently, possibly once a month or whenever the planner had the time. Given their extensive portfolio of over 2 million SKU-location combinations, this approach was neither efficient nor accurate.
- Complex supply chain. Their supply chain was highly complex, involving plants in different countries, some acting as flow-through warehouses. The lead time for raw materials and transfers between plants averaged a couple of weeks.
They also had multiple production options, including producing the same component at different plants or outsourcing certain processes, which added to the complexity of supply chain decisions.
- Overstock issues. They estimated their overstock to be around 20%, representing a significant potential for stock costs reduction. Their primary goal was to focus on stock planning and reduce these excess inventories.
What we did. We implemented SAP Integrated Business Planning (IBP) for Inventory to address their challenges. The project was a best practice pilot covering four plants and all SKUs produced at these plants, as well as the necessary raw materials.
Here’s how we approached the solution:
- We automated the safety stock planning process, making it fully dynamic and optimal. The recalculation of safety stock was performed weekly at the SKU level. This automation also extended the planning horizon, allowing them to see planned safety stock levels for the next six to nine months.
- Previously, our client relied on simple Excel-based stock analytics and general reporting in SAP BW. After the implementation, they had access to over 12 best practice analytical charts provided by SAP, along with an ABC classification of finished goods to prioritize stock planning based on product importance and sales volume.
- We helped establish an internal center of excellence for safety stock optimization. This center included IT consultants trained to configure IBP and key users who understood the business processes, system analytics and algorithms, and how to incorporate planning results into daily operations.
Challenges faced during implementation:
- We encountered difficulties with master data quality, as not all necessary data was present in the ERP system, and some data was incorrect or outdated. We advised the customer to appoint a dedicated person responsible for master data and involved planners in data verification processes.
- Forecasts received from their clients were often intermittent and could change with short notice. We advised to incorporate short-term forecasts and to work on past sales data to smooth sales history and improve forecast accuracy.
- The optimization algorithms used by the system were advanced and complex, making it difficult for users to understand the results. We conducted extra educational sessions to explain the logic and control parameters of the system and derived simple safety stock formulas for basic scenarios.
These improvements provided our client with the tools to effectively manage their inventory and reduce overstock.
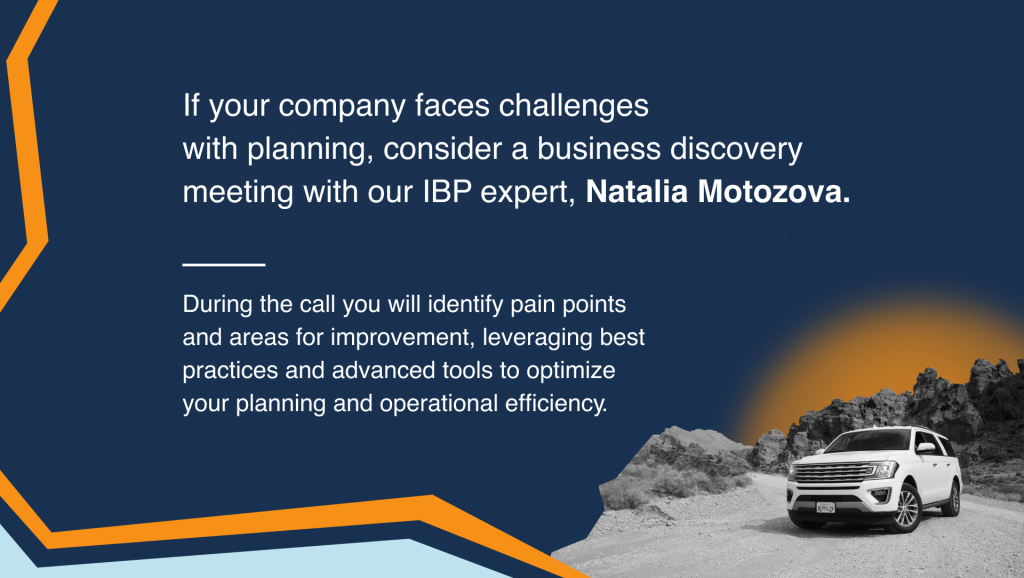
Key takeaways
-
How complex is SKU management in automotive manufacturing?
Managing numerous SKUs with various characteristics and production variants is highly complex. Advanced planning and automation are needed to efficiently handle Just-In-Time and Just-In-Sequence processes. -
Why are high service levels critical in the automotive industry?
Automotive suppliers must meet high service levels to avoid halting final assembly lines, which can lead to significant financial penalties. -
What challenges do automotive suppliers face with forecasting and planning?
Suppliers struggle with static safety stock calculations and managing extensive SKU-location combinations. Automation and dynamic planning can improve forecast accuracy and inventory management, reducing overstock issues. -
How do advanced planning solutions help automotive suppliers?
Tools like SAP IBP automate safety stock planning and provide analytical charts, improving inventory management and reducing overstock. -
What benefits do centers of excellence offer in inventory management?
An internal center of excellence helps in mastering advanced planning tools and algorithms, ensuring consistent, optimized safety stock levels. It also assists in training key users and integrating planning results into daily operations effectively.