2958
7 min
Safety stock calculation guide: how to reduce dead stock, and keep service level high

In this article, we explore the importance of safety stock, methods for its calculation, and strategies for reducing dead stock while keeping service levels high, with insights from Natalia Morozova, an IBP expert and architect at TeamIdea.
The importance of safety stock
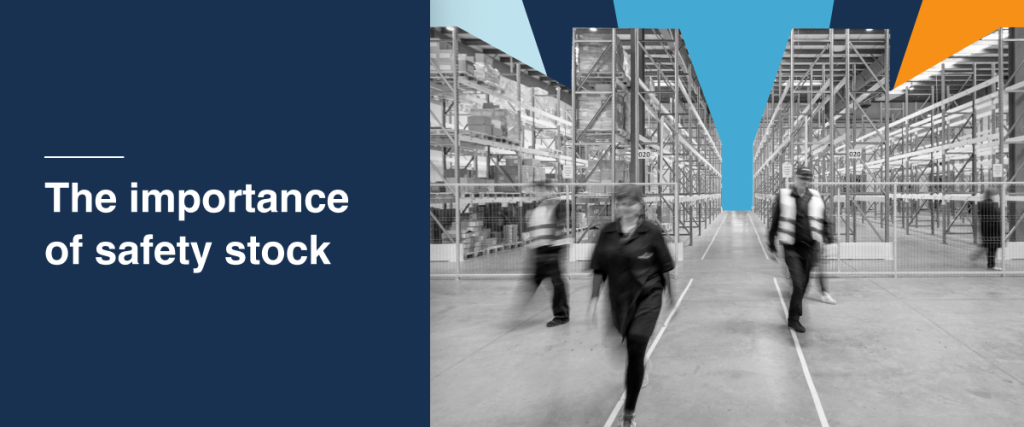
Safety stock is essential for covering requirements in case of supply chain disruptions. These disruptions can range from delays in shipping to unexpected increases in demand.
Safety stock acts as a buffer, ensuring that customer needs are met even when forecasts are not entirely accurate. For instance, even advanced forecasting techniques like machine learning can suffer from overfitting or inaccuracies in multi-linear regression models.
Maintaining a high service level is often the only way to ensure customer satisfaction, especially in industries like grocery retail, where a 50% service level might be a baseline.
Techniques for calculating safety stock
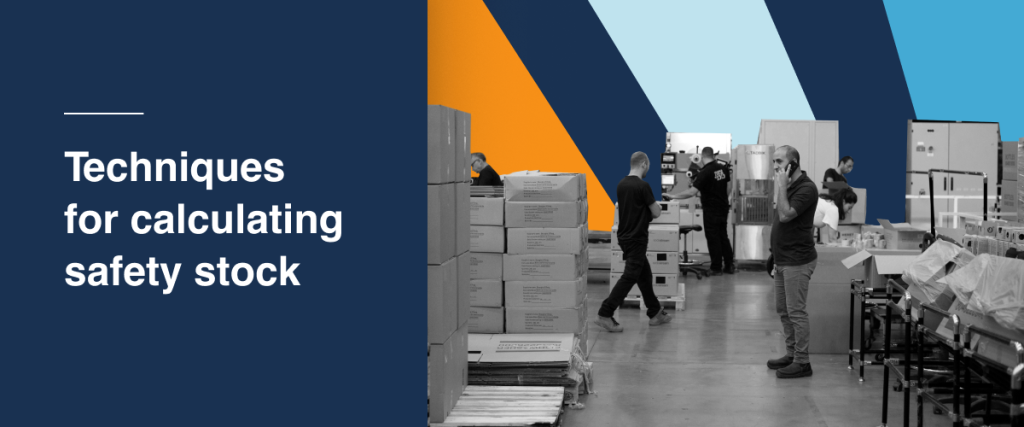
There are several methods for calculating safety stock, each suited to different business needs:
- Static Safety Stock in Pieces (PC). This method involves maintaining a fixed quantity of safety stock. It's a simple approach where a predetermined number of units are kept in stock regardless of demand variability.
- Static Safety Stock in Days. Here, safety stock is expressed in terms of the number of days' worth of inventory. For example, if a business decides to keep 10 days' worth of stock, it calculates the average daily usage and multiplies it by 10 to determine the safety stock level.
- Dynamic Safety Stock in Pieces per Period. This method adjusts the safety stock based on the period's demand. For example, in DIY retail, a 20% reduction in stock might be implemented dynamically based on sales patterns and seasonal variations.
Advanced dynamic safety stock calculation
For more sophisticated approaches, businesses can use advanced calculations involving statistical models. One example is using a gamma distribution to model demand uncertainty. This method considers several factors:- Service level coefficient (100%)
- Forecast error variance and demand mean. Metrics like MAPE (Mean Absolute Percentage Error) and MAD (Mean Absolute Deviation) are used.
- Period between replenishment and lead time
- Supplier lead time uncertainty
A common formula used for calculating safety stock is:
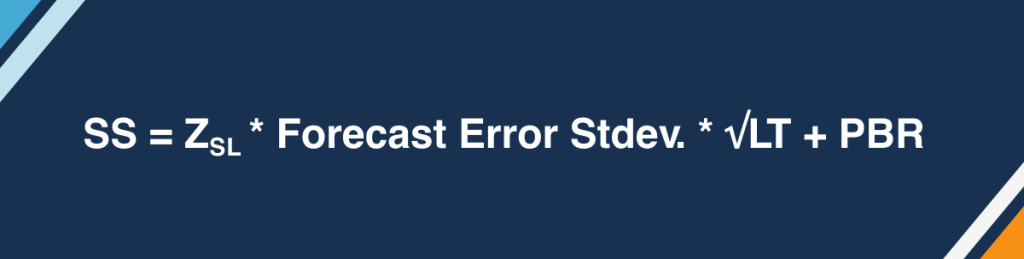
Let's break down this formula:
- Service Level Coefficient (Zsl). This represents the desired service level, expressed as a Z-score. For example, a 95% service level corresponds to a Z-score of 1,64. The higher the service level, the greater the safety stock required.
- Forecast Error Standard Deviation. This measures the variability in demand forecasts. A higher standard deviation indicates more uncertainty in demand, necessitating a higher safety stock. The standard deviation can be derived from historical forecast errors.
- Lead Time (LT). This is the time taken from placing an order to receiving it. The longer the lead time, the higher the safety stock needed to cover the period until the next replenishment.
- Period Between Replenishments (PBR). This is the time interval between successive inventory replenishments. Similar to lead time, longer periods between replenishments require higher safety stock to avoid stockouts.
Consider two scenarios with different forecast accuracies:
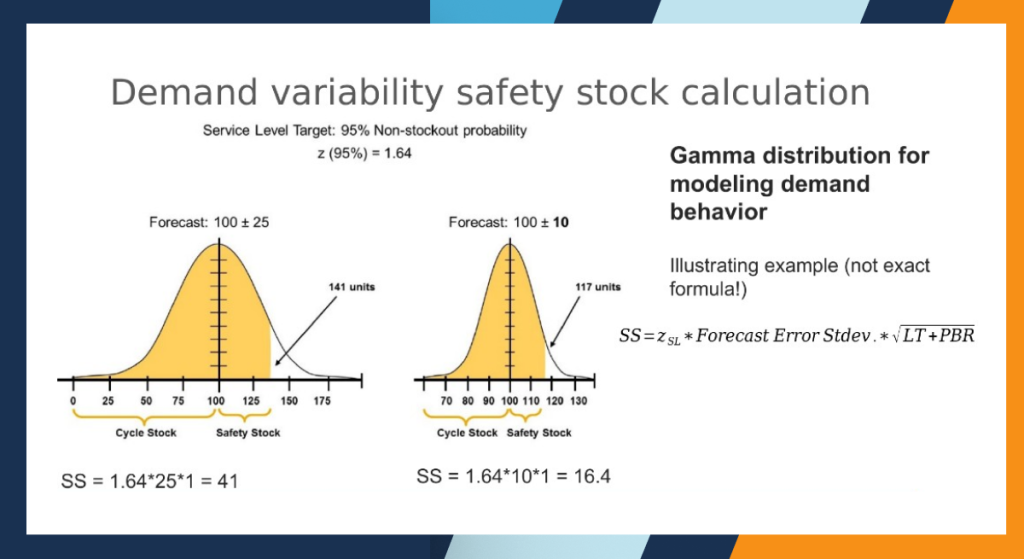
In the first scenario, due to higher forecast error, the required safety stock is 41 units. In the second scenario, with lower forecast error, the safety stock reduces to 16.4 units.
How to reduce dead stock
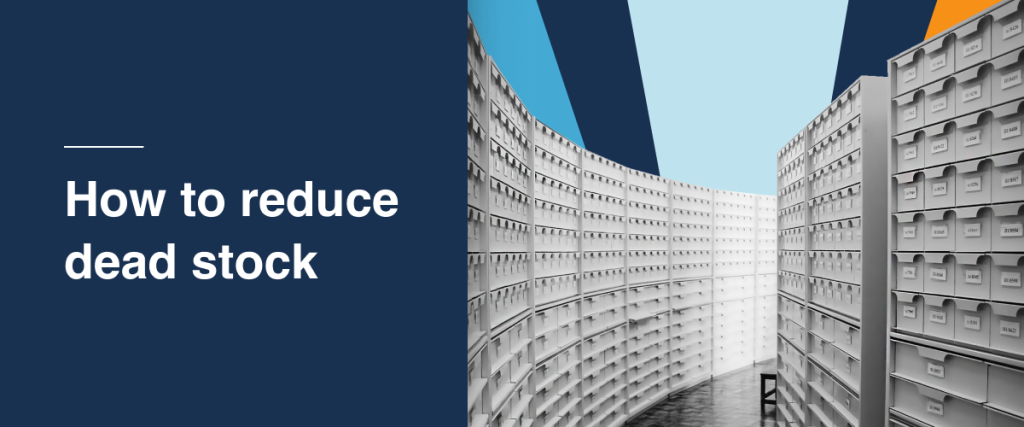
Dead stock is inventory that remains unsold and can tie up valuable capital. Here are some strategies to reduce dead stock while maintaining a high service level:
- Use dynamic safety stock. Adjusting safety stock based on real-time demand can prevent overstocking. By continuously analyzing sales data and adjusting inventory levels accordingly, businesses can better align stock with actual demand.
- Define target service levels correctly. Implementing methodologies like ABCXYZ analysis can help in setting appropriate service levels. This method categorizes products based on their importance (ABC) and demand variability (XYZ), allowing businesses to prioritize inventory management efforts.
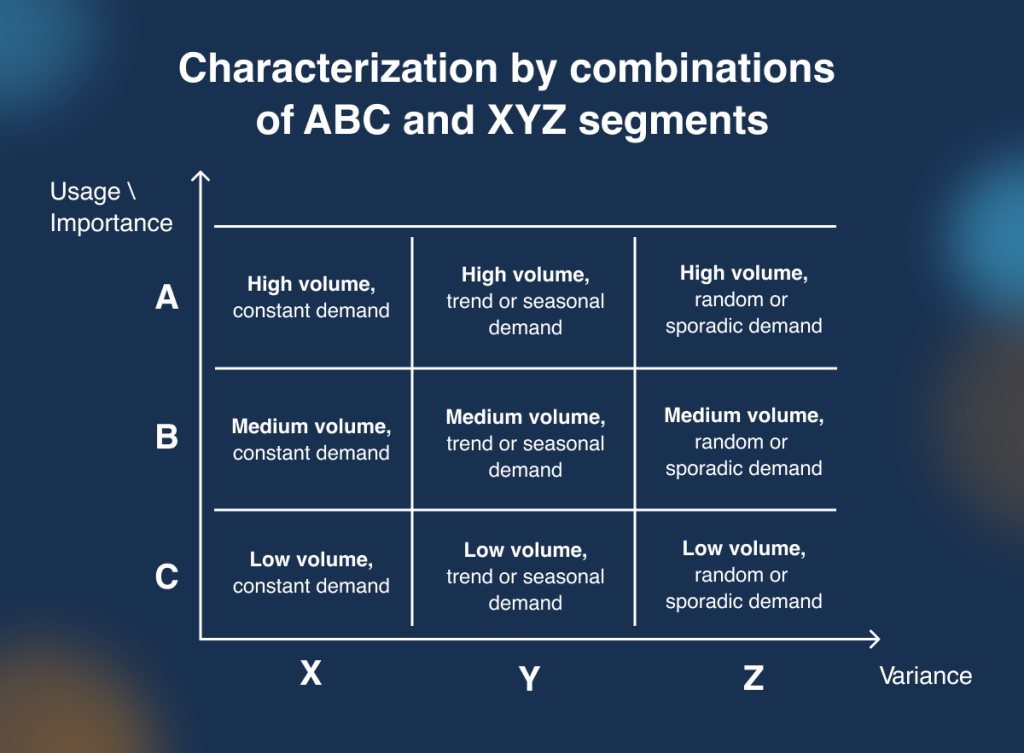
- Stock analytics. Regularly analyze stock quantities and prices per SKU and product categories using tools like heat maps. This analysis helps identify slow-moving items and potential dead stock, enabling proactive management actions.
- Logistical rounding. Compare minimum logistical units with demand and adjust the period between replenishments. Ensuring that order quantities align with actual demand reduces the likelihood of excess inventory.
- Avoid long lead times. Shorter lead times reduce the need for high safety stock levels. Working with reliable suppliers and optimizing procurement processes can help achieve this.
- Model optimal storage locations. Determine the best places to store safety stock to minimize storage costs and improve efficiency. Strategic placement of inventory can reduce lead times and enhance responsiveness to demand changes.
- Monitor manual adjustments. Keep an eye on manual adjustments made by users to ensure they align with overall inventory strategies. Regular audits and reviews of inventory adjustments can help maintain accuracy and prevent unintentional overstocking.
By using dynamic and advanced calculation techniques, businesses can better predict demand fluctuations and adjust their inventory accordingly. Additionally, strategies to minimize dead stock can free up capital and enhance overall efficiency. Implementing these practices ensures that businesses can meet customer demands consistently while optimizing their inventory management processes.
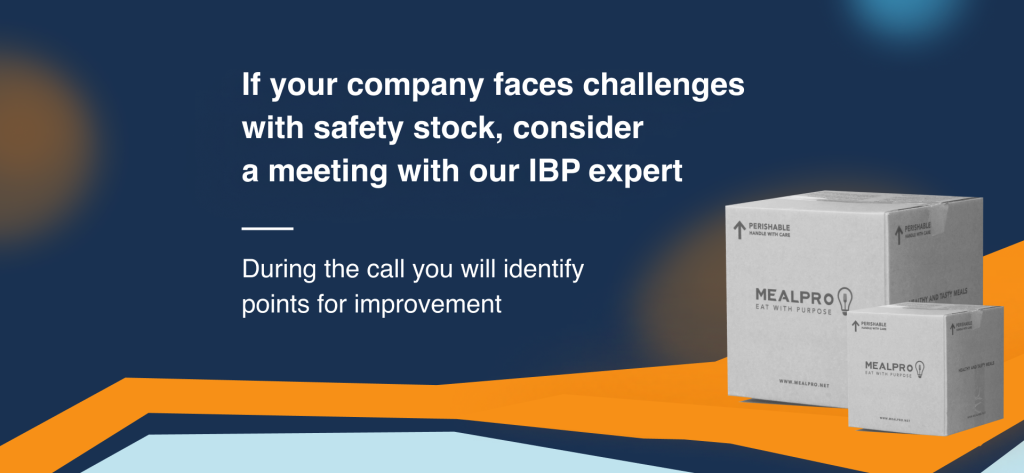
Key takeaways
-
What is the role of safety stock in supply chain management?
Safety stock acts as a buffer to cover supply chain disruptions such as shipping delays and demand spikes, ensuring customer needs are met. -
Why is maintaining high service levels crucial?
High service levels ensure customer satisfaction, particularly in competitive industries like grocery retail, where service levels can significantly impact customer loyalty. -
How can businesses reduce dead stock while maintaining service levels?
Strategies include adjusting safety stock dynamically, setting correct target service levels, regularly analyzing stock, optimizing logistics, shortening lead times, and strategically placing safety stock. -
What are the benefits of dynamic and advanced safety stock calculations?
These techniques allow businesses to better predict demand fluctuations, adjust inventory levels accordingly, reduce dead stock, free up capital, and enhance overall efficiency.