1541
5 min
Wave picking: warehouse tactic to balance order peaks and keep promises to the customers

Let's delve into how this method not only meets customer promises but also enhances warehouse productivity and efficiency. Stay tuned for insights from CEO of TeamIdea Group, Andrei Altabaev.
Let's dive into the terminology. What's a wave?
Easier to grasp with an example. Imagine a warehouse: work there isn't steady. Mondays are slow, Tuesdays see a sudden spike, Wednesdays quiet down again, Thursdays peak, and so on — each day bringing different volumes.
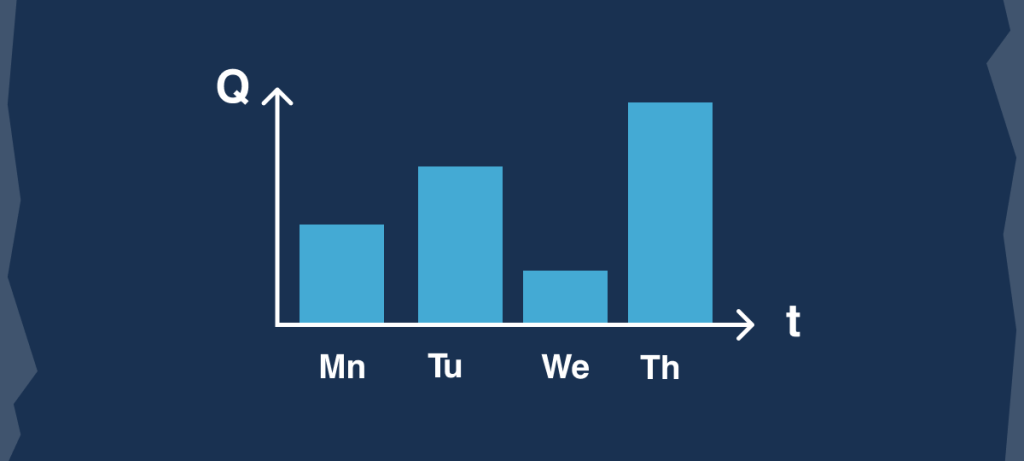
But if you've got 10 workers at the warehouse handling 100 orders a day, there's only so much they can handle. So, to keep up with commitments throughout the week, you've got to double or triple the resources on Tuesdays and Thursdays.
But you can't just magically conjure up extra hands out of thin air — that's not a solution. It's better to evenly distribute the workload over the week.
And that's where the term "wave" comes in. It's a batch of orders that needs to be shipped and picked around the same time. Each wave has its own capacity, helping to tackle the uneven workload at the warehouse.
How does wave picking help with unpredictable order spikes?
Let's stick with the example. We set up a kind of container, a "wave," for each day, capable of handling up to 100 orders.
So, if orders start pouring in and exceed the container's limit — say, it hits 101 — that extra order gets bumped to Tuesday.
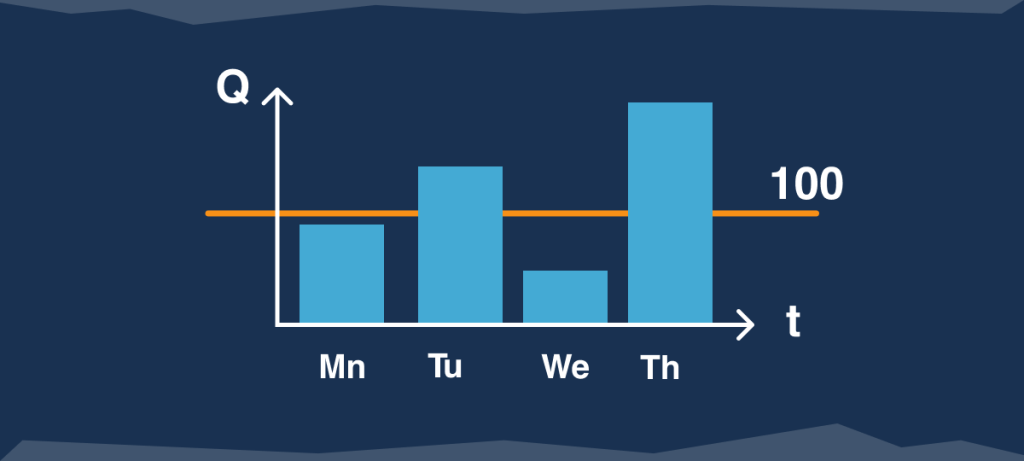
As soon as Tuesday's container fills up to 100, any new orders for that day get pushed to Wednesday. And so on: orders get shuffled around, their assembly and delivery dates sliding onto any available capacity in future waves. In the end, peaks get evened out, and the warehouse avoids underloading or overload situations. It's all about balancing the equation.
What other tasks does wave picking solve?
In addition to maintaining balance, there's also the task of optimization. Wave picking helps with that too.
How does a wave work? It all starts with the WHR — workhouse request, which is the customer order. Each order contains line items of what they've ordered. From each of these line items, one or multiple warehouse tasks are created.
A warehouse task is a clear and precise definition: from where, in what quantity, to where the product needs to be moved. For example, moving 3 units of a product from warehouse location A to location B.
And all 3 products could be stored in three different warehouse locations. Here, the task is to optimize order picking.
The WMS is nothing but the digitization of a physical reality of a warehouse within the system.
The system precisely knows how many meters it is from one warehouse location to another, where the picking zone is, how far a worker needs to walk, and where each item is located — it's all described. Based on all this data, the system starts to create optimal tasks for the staff — that's the first step, and prioritizes them — the second step.
The first task is to create an optimal route. Combining warehouse tasks helps with that. Based on the locations of the items, the system selects route points along a specific aisle and within the picking zone. Then it optimizes the sequence of movements so that the route can be completed in the shortest time possible.
These are very precise calculations. The solution uses the Manhattan metric: it considers the length of all the aisles to the next point and the speed of the worker or equipment. This is needed to calculate the order execution time. Let's say it's 5 minutes.
To this time, the time for other actions is added: reading the task, starting the forklift, and picking each item. This operation — organizing the optimal route and calculating time — is performed for each order.
As a result, each warehouse order has specific timings. The second stage begins — prioritization. The system builds a sequence of order execution so that they are all ready by the deadline and the wave is completed. And then all tasks are assigned to the staff in the form of standards.
And they start picking orders from this queue, according to the priorities.
How does wave picking help keep promises to customers?
First and foremost, this tool helps to avoid making agreements that are knowingly unfulfillable. If the warehouse can only handle a hundred orders and during an uncontrolled peak, it receives an additional fifty orders, there will definitely be quality issues.
Moreover, the algorithm makes work more efficient. A worker could spend the whole day walking around the warehouse picking one order. But it's much more efficient to move around the warehouse, picking items from different orders in the optimal route. This literally saves on mundane walking around the warehouse.
50% of warehouse operational expenses are related to order picking operations.
So, we've done all the calculations, planned everything out. And the next day, the truck didn't show up — it broke down. The sequence is changing: we no longer need to pick the first order; instead, we need to start with the second one.
And the system can quickly conduct a multi-factor analysis, consider the truck problem, and set new priorities. As a result, processes don't get interrupted.
Which warehouse should implement wave picking?
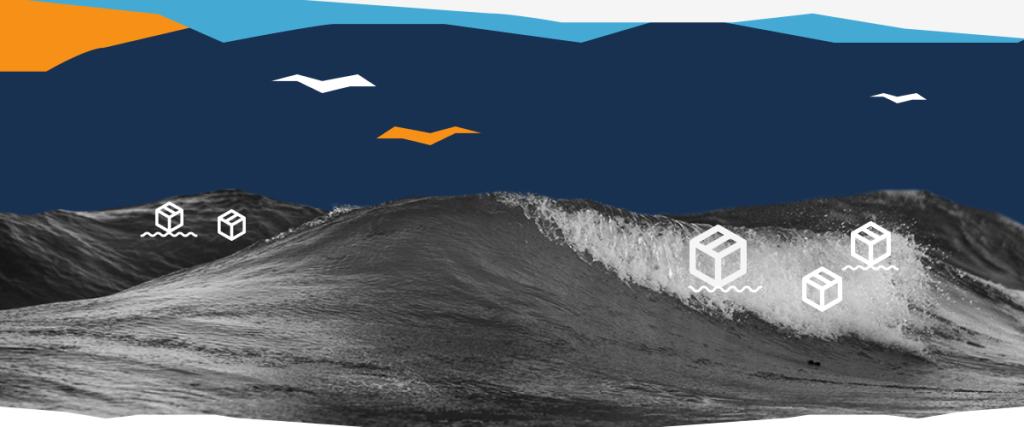
Wave picking is a hallmark of modern warehousing. Take a grocery warehouse, for instance. They do wave picking by pick-buy-line or pick-buy-shop.
What's that? For example, there are three stores, and waves are created for the warehouse based on them. On Monday, 1400 trucks are dispatched to store number 1: a wave is created to pick and load all the orders for this store, ensuring they're all ready by a certain time.
Let's look at a third-party logistics provider warehouse. The truck must arrive at a certain time. Orders also need to be picked and ready by a specific time, optimally, a wave suits here too. Then, consider an e-commerce store where you have a variety of products - wave picking is super relevant here.
However, for small warehouses, this tool is not necessary. For companies with less than 100 square meters, where one person knows everything, it's unnecessary.
In my opinion, this technology is a must-have to reach an industrial level. If you have at least a thousand square meters and a hundred SKUs, you simply must and should use wave picking, otherwise, you'll lose out in the competition.
Why is implementing wave picking a challenge for the warehouse operations director?
Because this process is tied to a very large number of parameters - it requires a lot of knowledge, skills, and efforts.
Let's start with managerial abilities. Usually, work in warehouses is done in a discrete manner. An employee gets a paper with one customer order with a certain number of items - and they go to pick them. Yes, you can glance over the whole paper and plan your actions. But it doesn't smell of optimality - the employee picks items in the sequence they think is best. In reality, a person cannot plot the truly best route.
When we start implementing waves, we create conditions where none of the employees know which order they are fulfilling. And this becomes a problem - you have to act strictly according to the system.
And from here comes the next challenge. To make everything work steadily, you need to correctly define the waves, break them down.
Here, business consulting is already needed. It's important for the warehouse not to choke, for it to cope with the task. And for this, the manager must provide all the historical data, reflecting on the warehouse's problems. If there's no experience in implementing automation, this step is quite difficult to pass.
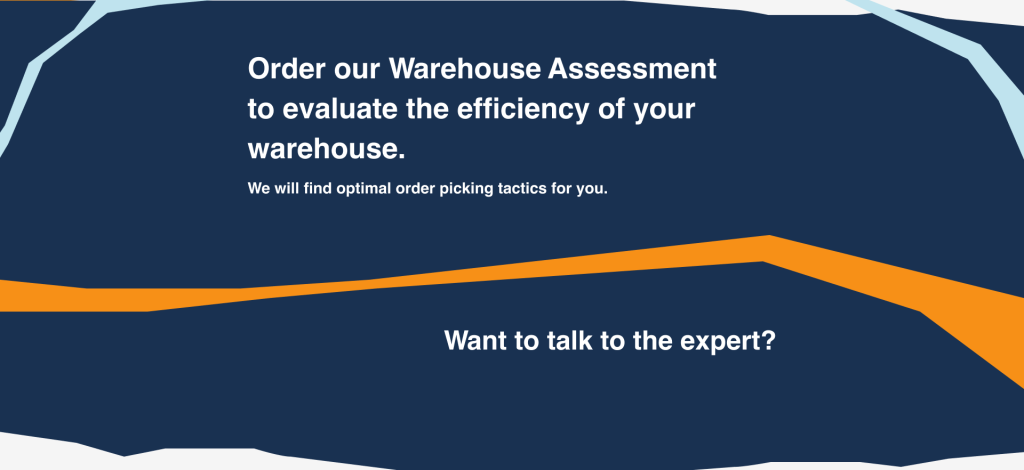
Key takeaways
-
What wave picking is?
Wave picking is a warehouse order picking method where orders are grouped into "waves." This approach balances the workload and improves efficiency. -
What tasks does wave picking solve?
Wave picking solves several issues. It handles unpredictable order spikes, optimizes picking routes and sequences, reduces unnecessary walking, and lowers operational costs. -
Keeping promises to customers.
Wave picking helps keep promises to customers. It ensures orders are completed on time, prevents warehouse overloads, and maintains high service quality. -
What about large warehouses?
Wave picking is ideal for large warehouses with at least 1000 square meters and over 100 SKUs. Smaller warehouses do not necessarily need this method. -
Implementing wave picking
Implementing wave picking requires strong management skills and precise planning. It involves analyzing historical data and may require business consulting.