1209
5 min
What Will Change in Your Warehouse After Implementing a WMS?

This trend is worth noting: if you look at market shifts, you’ll see rapid growth in e-commerce, which is closely linked to delivery services. Customers are becoming more demanding, expecting delivery within one or two days — often during specific time windows. Naturally, they also expect their orders to arrive accurately and without damage.
This demand is driving businesses to prioritize digital transformation to maintain their competitive edge. The global WMS market is projected to grow at an average annual rate of almost 13% from 2024 to 2032, according to “Fortune Business Insights”.
The statistics above indicate a steady interest in WMS adoption, particularly from retail, logistics, healthcare, manufacturing, FMCG, and pharmaceutical sectors. Let’s take a closer look at what a WMS is and the functionalities it offers.
WMS: What it is and The Core Functions Behind it
Traditional WMS functions cover essential warehouse operations, including:- Management of core warehouse data: from storage sections to queue types and storage bin types.
- Monitoring and control of all warehouse processes, such as inbound and outbound processing, as well as internal warehouse operations.
- Execution of material flow within the warehouse: picking, packing, labeling, weight checks, managing warehouse orders, batches, and serial numbers.
- Labor management and workflow support for the warehouse team.
- Automation of warehouse tasks using robots and automatic conveyors.
The features available in a WMS vary based on industry focus, provider, and the system’s evolution over time. An effective tool for evaluating and comparing WMS options is the 2024 Gartner Magic Quadrant.
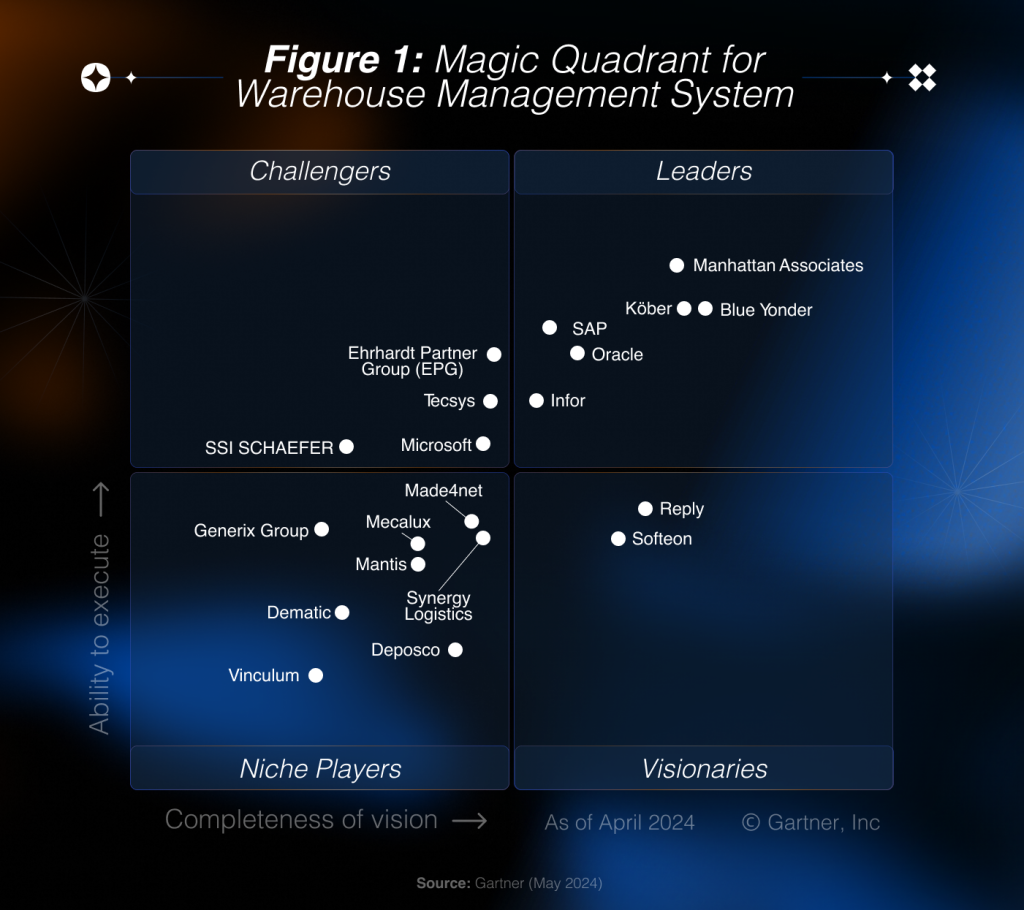
When reviewing the Gartner Magic Quadrant, you'll notice SAP EWM, SAP Extended Warehouse Management, a leading WMS solution.
SAP EWM is a reliable, high-performance solution designed for large-scale retail, FMCG, pharma, and logistics companies. Here some of the system advantages:
- Multi-picking, wave picking, and efficient queue management for warehouse orders.
- Easy integration with multiple robotics vendors.
- Yard management functionality.
- Exception handling for warehouse operations.
- Cross-docking support.
One of the unique advantages of SAP EWM is its seamless integration within the SAP ecosystem, a significant benefit for companies already using SAP S/4HANA. For those looking to simplify their system landscape, there’s also an embedded SAP EWM within the SAP S/4HANA system.
Once you've compared various options, the next question to ask: is your company ready for a WMS implementation?
Checklist: When it’s Time to Implement a WMS
The need becomes clear when your company faces challenges.- You are planning to significantly increase the number of distribution centers (DCs) in the next 1-2 years, but opening new DCs is difficult because the processes are not standardized.
- Your customers are dissatisfied with your OTIF (On-Time, In-Full) performance.
- You experience high return rates due to picking errors.
- Your competitors offer faster order fulfillment, and you need to accelerate your warehouse operations to maintain your market share.
- Your warehousing costs are high due to inefficient use of space and excessive labor expenses.
- It takes over two weeks to train new warehouse staff, and you’re struggling to find qualified workers, making your operations vulnerable to fluctuations in the labor market.
- Many stock items are spoiled or written off because of inadequate shelf-life management and inconsistent storage conditions.
According to TeamIdea’s experience, if your total warehouse area exceeds 5,000 square meters and your outbound flow exceeds 500 cartons (or other handling units) per week, it’s time to implement a WMS. With this scale of business, digital transformation can deliver rapid ROI, providing benefits to your bottom line.
How WMS Drives Business
As many companies worldwide have already implemented WMS, there are established benchmarks for the business gains typically achieved.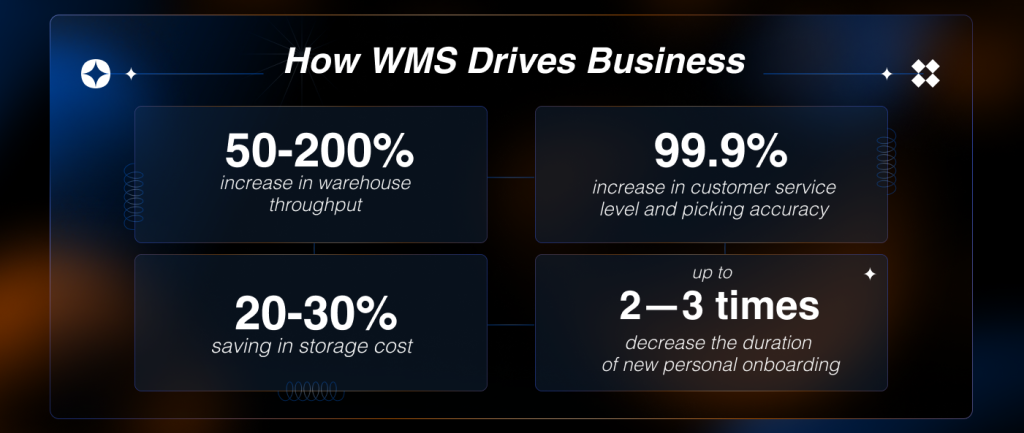
Here are some of the most notable benefits:
- A 50-200% increase in warehouse throughput.
- A 20-30% saving in storage cost.
- Increase in customer service level and picking accuracy to 99.9%.
- Decrease the duration of new personal onboarding up to 2—3 times.
One of the operational improvements is automation in picking — a step in order fulfillment. One approach commonly used to increase throughput is wave picking.
This method enables multiple orders to be picked at the same time, rather than picking each item for an order individually, which can be time-consuming. Wave picking groups items from the same inventory for multiple orders, allowing them to be picked together before moving to the packing stage. WMS optimizes this process by setting priority rules and sequences, which increases the number of orders processed per day.
WMS helps businesses make the most of their available warehouse space, leading to significant cost savings. By managing different storage areas — from mezzanine racks and refrigerated spaces to receiving and dispatch zones — WMS offers real-time insights into how space is being used.
Often, warehouses are not fully utilized, but with WMS, space efficiency improves, allowing for more items to be stored and reducing the overall cost per unit.
WMS boosts picking accuracy and reduces errors by tracking inventory with BIN codes and batch numbers. This functionality ensures that items are correctly received, picked, packed, and shipped.
With WMS, core operations can also be automated using conveyors and robots, reducing the risk of mistakes that could lead to returns due to incorrect order contents.
For perishable goods, shelf-life tracking is important. WMS monitors the remaining shelf life of each batch and SKU to ensure customers receive fresh products.
WMS streamlines workflows and provides easy-to-use tools that guide new employees through their tasks. This efficiency reduces the time needed to onboard new warehouse personnel, lowering the risk of errors and operational disruptions. Managers also gain tools for tracking performance and managing exceptions, ensuring a smooth transition for new team members.
Case: WMS Implementation for Exist — a Major Online Retailer of Auto Service Parts
Let’s take a real-world project from TeamIdea’s experience.The company: Exist, ecom retailer of auto parts with a customer base of over 6 million.
Company overview (point A):
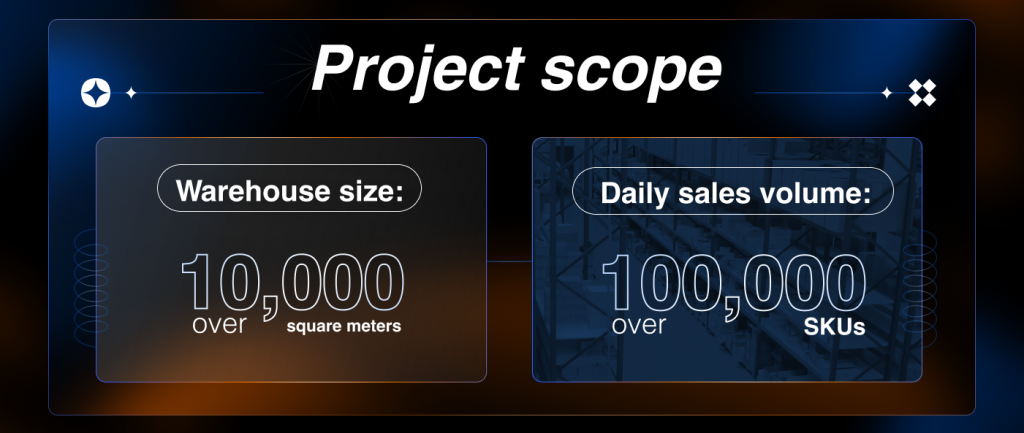
- Warehouse size: over 10,000 square meters
- Daily sales volume: over 100,000 SKUs
Project objectives (point B):
- Achieve 2-3 times higher throughput on new warehouse with WMS in place.
- Achieve more than 50% of sales directly from the Exist warehouse (as opposed to suppliers), leveraging shorter lead times for customers.
- Optimize storage and implement flexible pricing based on fulfillment costs.
Recognizing that an advanced WMS was essential to meet these goals, Exist conducted a market review and chose to implement SAP EWM with TeamIdea, an SAP Platinum Partner.
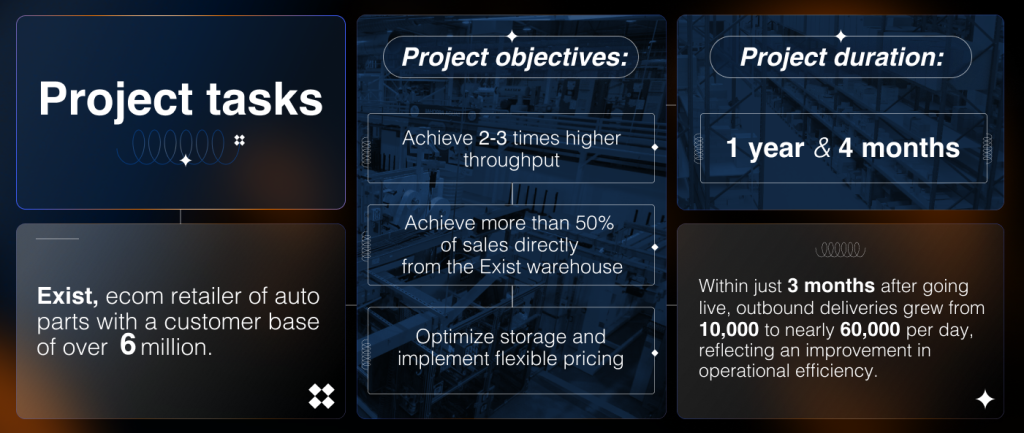
The project presented several challenges:
- Simultaneous implementation. The project required the integration of both SAP ERP and SAP EWM, demanding high levels of coordination and data synchronization between the systems.
- Tight timeline. With a tight project deadline, the team was tasked with deploying both systems in just 1 year and 4 months.
Within just 3 months after going live, outbound deliveries grew from 10,000 to nearly 60,000 per day, reflecting an improvement in operational efficiency.
How to Measure Expected Benefits
Estimating the ROI of WMS implementation can be done at a high level using a straightforward approach. Here’s how you can quickly evaluate the potential benefits for your company.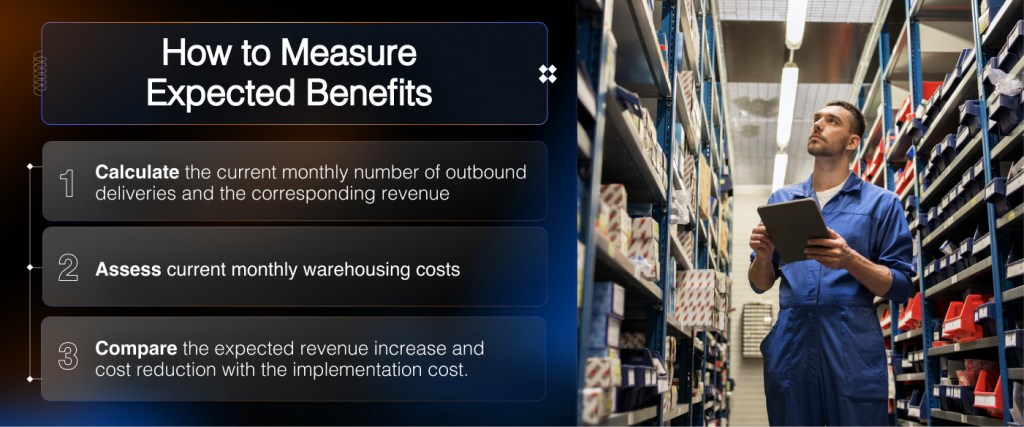
1. Start by calculating the current monthly number of outbound deliveries and the corresponding revenue generated from fulfilling these deliveries. Then, estimate the potential increase in both metrics:
- +50% increase if you currently do not have a WMS.
- +20% increase if you already have basic WMS functionality but are planning to upgrade to a more advanced solution like SAP EWM.
2. Next, assess your current monthly warehousing costs, including expenses like warehouse staff salaries, resource utilization, and other operational costs. Based on the efficiencies gained through automation, improved order management, and better space utilization, you can expect a 20% reduction in these costs.
3. Compare the expected revenue increase and cost reduction with the implementation cost.
- Add up the expected revenue boost and cost savings, and compare that with the total cost of implementation and licensing.
- For example, if you expect a monthly revenue increase of $100,000 and the cost of license and implementation is $1 million, the ROI would take 10 months to recover.
If you’re unsure whether your company is ready for WMS implementation or want to gauge your expected ROI more precisely, we offer a quick 5-minute readiness check. Simply provide your contact information, and we’ll reach out to you via email.
For a more in-depth evaluation of your company’s readiness and a detailed ROI calculation, feel free to book a business discovery meeting with TeamIdea.
Key takeaways
-
The growth of e-commerce and rising customer expectations for faster, error-free deliveries are pushing businesses toward digital transformation.
A WMS enables companies to stay competitive by improving efficiency and service quality. -
WMS implementation can boost throughput by 50–200%, reduce storage costs by 20–30%, and increase picking accuracy to 99.9%.
Additional advantages include faster onboarding and improved customer satisfaction. -
A WMS manages core warehouse data, automates tasks like picking and packing, and integrates with robotics for enhanced efficiency.
Advanced solutions like SAP EWM offer yard management, cross-docking, and seamless integration with SAP S/4HANA. -
Signs of WMS implementation readiness include difficulty standardizing processes, high return rates, rising costs, and long onboarding times for new staff. For warehouses exceeding 5,000 square meters or 500 weekly cartons, a WMS delivers measurable ROI.
-
How can companies measure the ROI of a WMS?
Calculate potential revenue increases and cost reductions. Compare these gains with the total implementation cost to evaluate ROI.