1515
10 min
WMS vs. ERP: Which System Suits Your Warehouse Best?

To illustrate how WMS works in a warehouse, we’ll use photos from TeamIdea’s project with Sberlogistics, one of the largest 3PL operators in the CIS, which processes over 150,000 orders daily with a WMS solution based on SAP Extended Warehouse Management.
The Core Difference
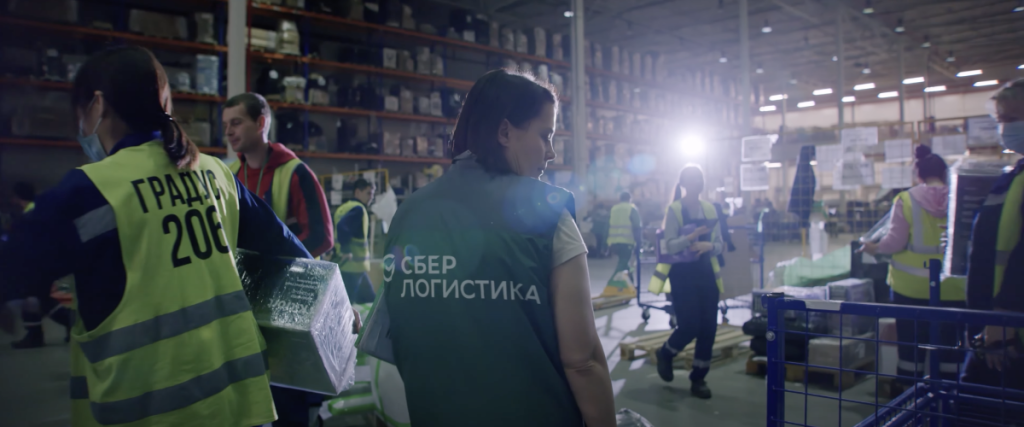
Let's start with the main difference: WMS can create work tasks in a warehouse, directing workers on where to move goods, when to pick items, and how to organize inventory efficiently.
An ERP system focuses more on administrative and planning functions like assigning storage locations (bins) and managing user roles but lacks the operational depth for real-time task management. This makes ERP more suitable for overseeing procurement and inventory processes rather than daily warehouse operations.
Below is a comparison between a warehouse using basic warehouse management tools embedded in an ERP (SAP S/4HANA) system and one with advanced SAP Extended Warehouse Management (SAP EWM).
Procurement
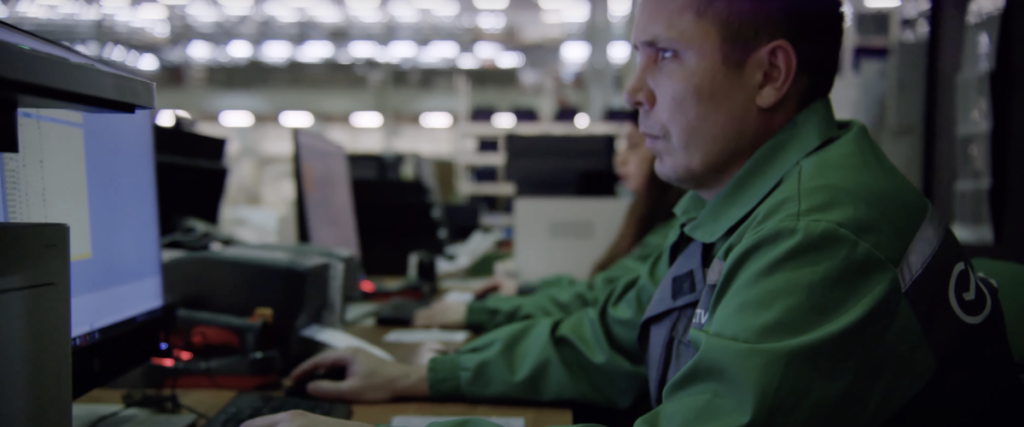
In the procurement stage, the ERP system takes the lead, managing the full process: supplier selection, purchase order creation, approvals, and financial transactions. However, the value of WMS becomes clear in the subsequent stages — handling, storing, and managing goods inside the warehouse.
Goods Receiving and Unloading
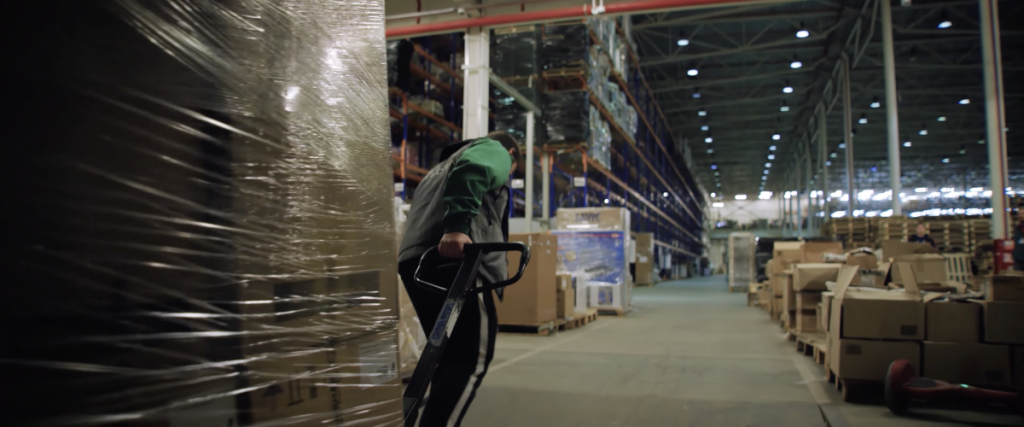
ERP-Embedded Functionality: The ERP system creates receipts based on shipment notifications and can provide a list of locations where the product can be stored. It typically does not handle volume management; it only allows specifying the capacity of a location in units. Much of the verification and counting is done manually by warehouse staff. This may lead to errors, resulting in discrepancies between what is physically received and what is recorded in the system.
Warehouse with SAP EWM: Automated receiving process. When a shipment arrives, the system retrieves order data and directs vehicles to unloading bays. WMS can track the percentage of space utilization, inventory needs, and current reserves. It can offer to split the same product from a shipment into different containers and create a specific placement plan for each.
Inspection and Scanning
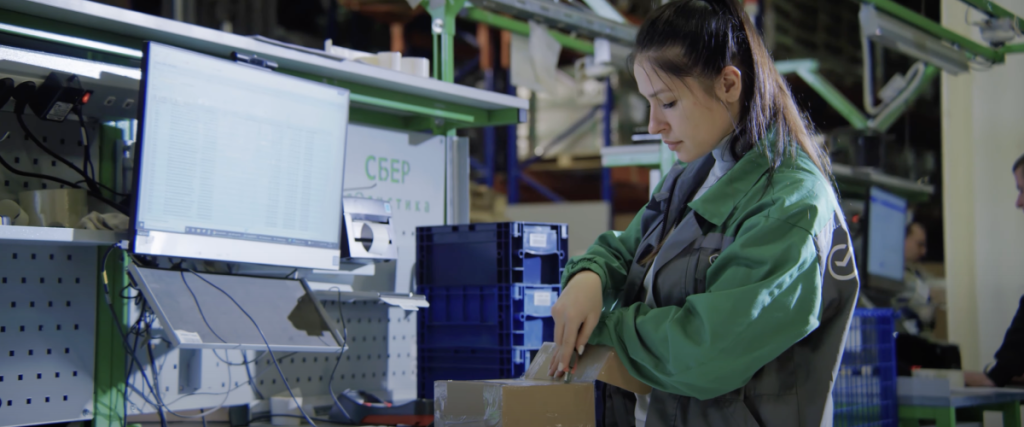
ERP-Embedded Functionality: Quality inspection in a ERP-managed warehouse relies heavily on manual processes. Scanning is often performed using separate systems or logged manually, creating time-consuming delays. That leads to slower processing times and a higher risk of defects going unnoticed.
Warehouse with SAP EWM: Quality inspection is integrated directly into the receiving workflow. As items are unloaded, they undergo immediate inspection, scanning, and sorting into appropriate containers. The system records inspection results and tracks quality issues, ensuring that only defect-free products move forward in the process.
Storage Management
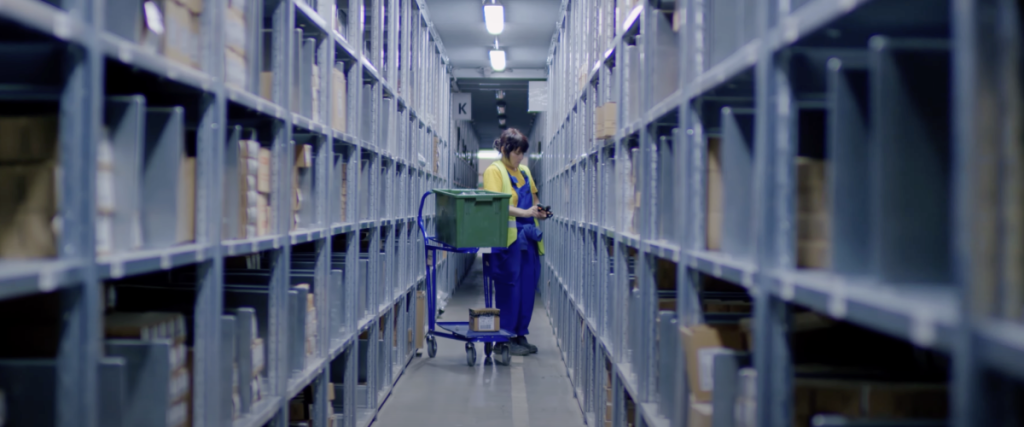
Basic ERP-Embedded Functionality: Storage in a basic ERP system is static, relying on fixed storage locations. If a worker cannot use the assigned bin, the ERP system cannot quickly suggest another one. If an employee tries to place an item in what appears to be an empty bin, the ERP will not check for other planned placements in that bin and will not prevent the action if there are. Workers must often decide by themselves where to place the items.
Warehouse with SAP EWM: Storage tasks are created dynamically based on real-time data. The system considers item compatibility, weight, and size to determine the most efficient storage location and builds the route for the worker. This approach maximizes space utilization and minimizes the time workers spend moving between storage locations.
Order Picking and Packing

Basic ERP-Embedded Functionality:
Order Picking: In a warehouse using basic ERP tools, the system provides an address for picking, but it lacks real-time information about the inventory. The address might contain a mix of items or none of those on the picking list. Several employees often arrive at the bin at once only to find they can’t complete the pick. In another case a worker needs to collect apple juice. The system might direct them to an address where multiple types of juice are stored. The worker sees a label that says "apple" and assumes it's correct, but without precise system guidance, they might mistakenly pick an apple-pear instead of pure apple juice.Packing: Packing in a basic ERP-managed warehouse is also manual. Workers choose packaging based on their judgment rather than system-driven recommendations. This might result in the use of standard-sized boxes that are often ill-suited to the items, leading to wasted space, higher shipping costs, and inconsistent packaging practices. The manual nature of the packing process further reduces efficiency.
Warehouse with SAP EWM:
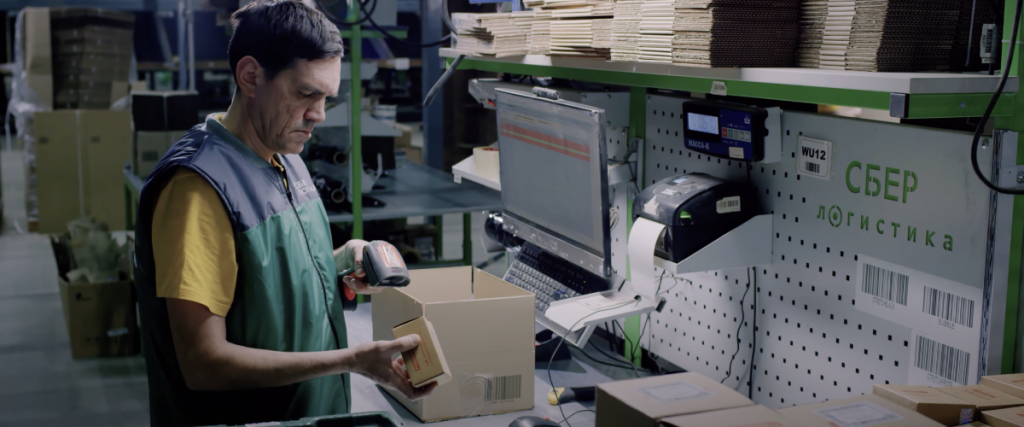
Order Picking: In a warehouse using SAP EWM, order picking is optimized through automated picking tasks that guide workers along the most efficient routes. The system ensures that the item picked is the one required for the specific order.
Replenishment: If SAP EWM detects that a product in the picking zone is running low or insufficient for all orders in progress, it automatically creates a replenishment task. A forklift brings down a pallet and places it in the picking zone, creating reserves and assigning picking tasks without manual intervention.
Packing: The system enhances packing by suggesting the ideal box size based on the item's dimensions and the overall order volume. This approach optimizes space usage and reduces shipping costs. Automated scanning verifies the contents before dispatch.
Physical Inventory
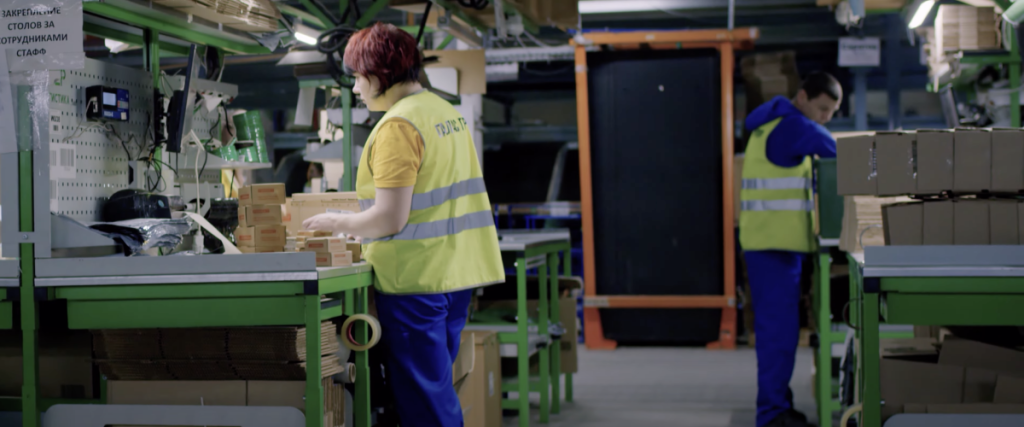
Basic ERP-Embedded Functionality: Physical inventory in an ERP-managed warehouse requires operations to stop to ensure data accuracy, as the system cannot handle live updates during the count. While this pause helps prevent errors, it is time-consuming and disrupts warehouse flow, failing to account for any movements made during the process.
Warehouse with SAP EWM: SAP EWM enables physical inventory without halting operations, thanks to real-time inventory adjustments. The system updates counts dynamically, capturing any picking, placing, or moving of items as they happen.
Sorting and Consolidation
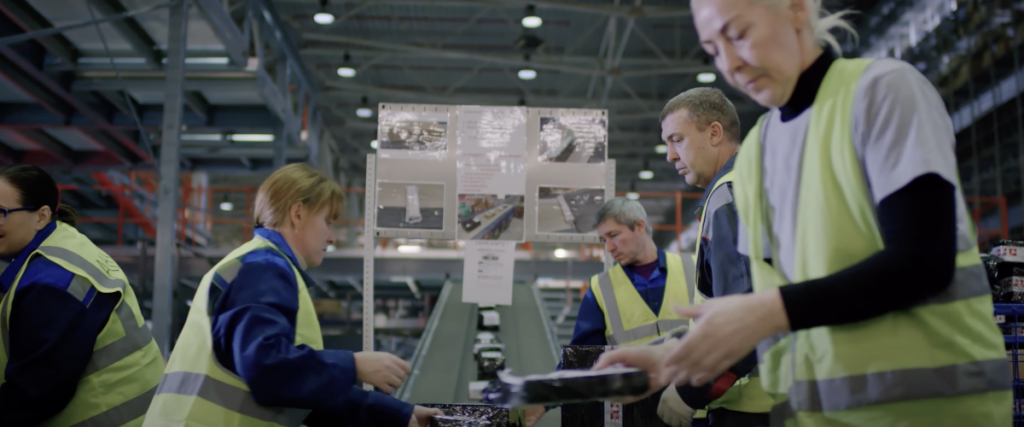
Basic ERP-Embedded Functionality: Sorting in a warehouse using basic ERP tools relies heavily on manual labor. Workers sort deliveries based on shipping destinations with minimal system support, leading to delays and a higher risk of errors. This manual process requires workers to physically handle and organize deliveries without the assistance of advanced automation.
Warehouse with SAP EWM: A warehouse with SAP EWM benefits from both manual and automated sorting options. High-performance sorting conveyors, when used, integrate with SAP EWM to automatically sort deliveries by destination, processing thousands per hour. The system directs each delivery to the correct location using real-time data.
Even in warehouses without conveyors, SAP EWM manages delivery flow by providing precise placement instructions based on real-time information. This approach reduces manual effort and minimizes sorting errors.
Outbound Delivery
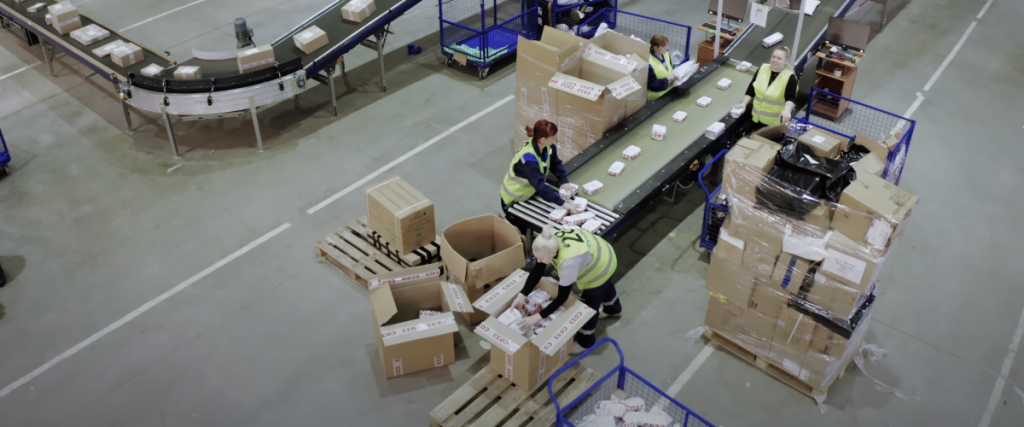
Basic ERP-Embedded Functionality: The outbound delivery process in a basic ERP-managed warehouse is largely manual, relying on warehouse staff for verification and organization.
Warehouse with SAP EWM: SAP EWM streamlines the outbound delivery process with automated verification. Each delivery is scanned with RF-guns and checked against system records before being loaded onto transport vehicles, ensuring all items are correctly accounted for and significantly reducing errors.
When Does a Warehouse Need a WMS Solution? 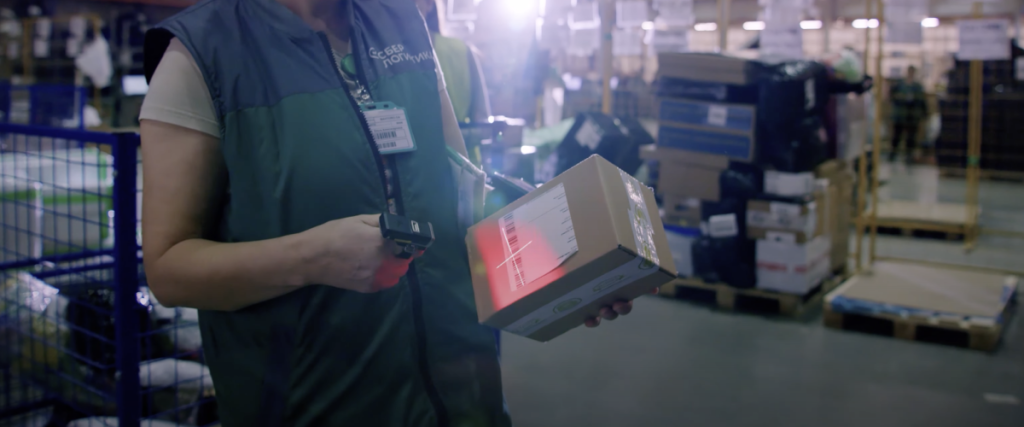
A well-implemented WMS solution can be transformative, turning your warehouse into a value-adding part of the supply chain. It's not just about the technology but about enhancing the processes that it supports. By automating routine tasks and providing actionable insights, WMS improves accuracy, reduces errors, and streamlines operations. However, the true impact of it is realized only when it is closely aligned with the specific needs and workflows of the warehouse, enabling better decision-making and more efficient use of resources.Below are the decisive criteria that must be taken into account when considering the implementation of a warehouse management system like SAP EWM.
Number of Operations: The volume of tasks per period or per employee is critical. If your warehouse handles hundreds or thousands of daily operations such as picking, packing, or shipping, a WMS solution is likely necessary. For instance, a 300-square-meter warehouse managing several hundred picks per day benefits from automation , whereas a larger warehouse (20,000–30,000 square meters) with fewer than 100 shipments daily does not require it.
Warehouse Size and SKU Management: Warehouse size alone does not determine the need for automation . A smaller warehouse (300 square meters) with thousands of small items and high daily order volumes needs a WMS solution, while a larger warehouse (30,000 square meters) with only 20 SKUs and few orders per day does not.
SKUs vs. Daily Orders: If your warehouse has thousands of SKUs but processes less then 100 orders daily, manual methods suffice. However, if daily picking reaches 200–300 SKUs with thousands of order lines, WMS implementation becomes justified.
Staff Efficiency and Process Optimization: Growing numbers of warehouse workers with growing amounts of mistakes in orders and customer complaints usually indicate business process issues rather than just the need for automation. It is important to optimize processes first; WMS enhances structured workflows and reduces time spent on tasks such as routing and placement.
Special Inventory Requirements: Managing batches, expiration dates, or specific item attributes makes SAP EWM crucial for maintaining accuracy and efficiency. No ERP solves this.
Conclusion
ERP and WMS systems serve distinct roles within warehouse operations. ERP systems primarily focus on administrative and accounting tasks, offering basic inventory management capabilities that can handle simpler, low-volume processes. While ERP can manage some warehouse activities, it often relies heavily on manual input and lacks the operational depth required for detailed, real-time task management.WMS solutions like SAP EWM, on the other hand, are specifically designed to optimize warehouse management: from receiving and storage to picking, packing, sorting, and outbound delivery. They address the complex, high-volume demands that basic ERP systems struggle to manage effectively, particularly when precision, speed, and accuracy are critical.
Relying solely on an ERP system can lead to slower operations, lower quality, and a higher risk of errors, especially as warehouse activity increases. These limitations are manageable only when warehouse complexity and activity levels remain low. However, as productivity grows, so does the potential for operational challenges, inefficiencies, and errors that can disrupt the flow of goods and impact overall business performance.
When the volume and complexity of operations exceed the capabilities of basic ERP, transitioning to a WMS becomes essential. SAP EWM, as the best-in-class solution, provides the scalability needed to support growing businesses, reducing manual tasks, improving accuracy, and significantly boosting operational efficiency.
For warehouses aiming to scale, enhance service quality, and maintain a competitive edge, implementing WMS is not just an upgrade — it's a strategic move that aligns with long-term growth and performance goals.